Phosphorylated polymerization polymer dispersant and its preparation method
A technology of polymer dispersant and phosphate ester, applied in chemical instruments and methods, botanical equipment and methods, biocides, etc., can solve problems such as poor dispersion effect, improve ionization degree and hard water resistance, and improve The effect of dispersion performance
- Summary
- Abstract
- Description
- Claims
- Application Information
AI Technical Summary
Problems solved by technology
Method used
Examples
Embodiment 1
[0011] A phosphated polymeric polymer dispersant, the comonomer composition and material percentages are: phosphated hydroxyethyl methacrylate 5.0%, methacrylic acid 95.0%.
[0012] The preparation method of this dispersant is:
[0013] (1) Add 5.0g of ethanol into a 250mL reactor, stir and wash it, let it go, heat and evaporate to dryness, take out the moisture in the reactor, add 13.0g (0.10mol) hydroxyethyl methacrylate into the reactor, Raise the temperature to 35°C, add 17.0g (0.12mol) phosphorus pentoxide in 17 times under vigorous stirring, the addition time is controlled at 1.5h, after the addition is completed, raise the temperature to 60°C, and react for 2.0h Add methacrylic acid into the reactor and stir evenly; (2) Add 205.0g of water and 10.0g of isopropanol into a 1000mL reactor, raise the temperature to 95°C, and dropwise add the above monomer mixture and 193.6g of 5.0% super Ammonium sulfate aqueous solution, dropwise for 2.0h, continue to react for 3.0h; (3) ...
Embodiment 2
[0020] A phosphated polymeric polymer dispersant, the comonomer composition and material percentages are: 25.0% phosphated hydroxypropyl methacrylate, 75.0% methacrylic acid.
[0021] The preparation method of this dispersant is:
[0022] (1) Add 4.0g of isopropanol into a 250mL reactor, stir and wash it, let it go, heat and evaporate to dryness, take out the moisture in the reactor, and add 36.04g (0.25mol) of hydroxypropyl methacrylate into the reactor In the middle, the temperature was raised to 35°C, and 42.58g (0.30mol) of phosphorus pentoxide was added in 25 times under vigorous stirring, and the addition time was controlled at 2.0h. mol) methacrylic acid was added to the reactor and stirred evenly; (2) 180.0g water and 1.0g thioglycolic acid were added to a 1000mL reactor, the temperature was raised to 85°C, and the above monomer mixture and 103.0g 8.0% Aqueous solution of ammonium persulfate. The dropping time is 1.8h, and the reaction is continued for 3.0h; (3) Afte...
Embodiment 3
[0028] A phosphated polymeric polymer dispersant, the comonomer composition and material percentages are: 50.0% phosphated hydroxypropyl acrylate, 5.0% maleic anhydride, and 45% acrylic acid.
[0029] The preparation method of this dispersant is:
[0030] (1) Add 4.5g of isopropanol into a 250mL reactor, stir and wash, let it go, heat and evaporate to dryness, take out the moisture in the reactor, add 65.07g (0.50mol) of hydroxypropyl acrylate into the reactor, Raise the temperature to 35°C, add 85.16g (0.60mol) phosphorus pentoxide in 30 times under vigorous stirring, and control the addition time at 3.0h. Anhydride and 32.43g (0.45mol) acrylic acid were added to the reactor and stirred evenly; (2) 330.0g water and 8.0g sodium bisulfite were added to a 1000mL reactor, the temperature was raised to 90°C, and the above monomers were added dropwise to it at the same time The mixture and 90.0g of 10.0% ammonium persulfate aqueous solution were added dropwise for 3.0 hours, and t...
PUM
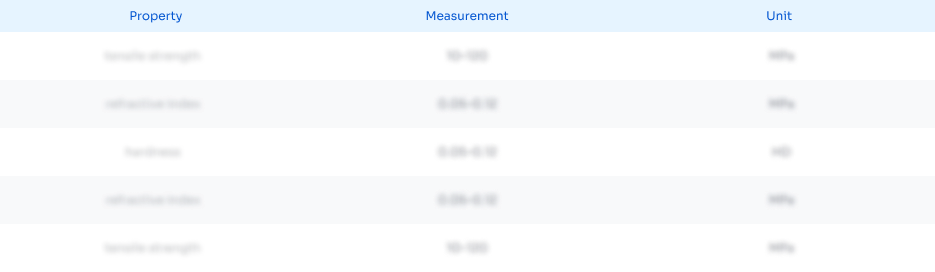
Abstract
Description
Claims
Application Information

- R&D
- Intellectual Property
- Life Sciences
- Materials
- Tech Scout
- Unparalleled Data Quality
- Higher Quality Content
- 60% Fewer Hallucinations
Browse by: Latest US Patents, China's latest patents, Technical Efficacy Thesaurus, Application Domain, Technology Topic, Popular Technical Reports.
© 2025 PatSnap. All rights reserved.Legal|Privacy policy|Modern Slavery Act Transparency Statement|Sitemap|About US| Contact US: help@patsnap.com