Preparation method of dialkyl phosphinic acid and salt thereof
A technology of dialkyl phosphinic acid and dialkyl phosphine, which is applied in the field of preparation of dialkyl phosphinic acid and its salts, can solve the problems of easy quenching and deactivation of free radical initiators, long reaction period, etc. The effect of high purity and simple process flow
- Summary
- Abstract
- Description
- Claims
- Application Information
AI Technical Summary
Problems solved by technology
Method used
Image
Examples
Embodiment 1
[0044] Example 1: Preparation of high concentration hypophosphorous acid
[0045] Get 400.1g mass fraction to be 50% hypophosphorous acid and 250ml cyclohexane, add in the reaction bottle that oil-water separator and condenser are housed, fill up cyclohexane in oil-water separator;
[0046] Under the protection of nitrogen, heat and stir until azeotropic for about 2 hours, and discharge the water separated at the bottom of the oil-water separator in stages; add the solution in the reaction bottle to the separatory funnel to separate to obtain 249.8 g of the lower layer liquid, and use acid-base titration to obtain the acid content For: 80.25% (mass fraction).
Embodiment 2
[0047] Example 2: Preparation of high concentration hypophosphorous acid
[0048] Get 400.1g mass fraction to be 50% hypophosphorous acid and 250ml cyclohexane, add in the reaction bottle that oil-water separator and condenser are housed, fill up cyclohexane in oil-water separator;
[0049] Heat and stir under nitrogen protection until azeotropic for about 3 hours, and discharge the water separated at the bottom of the oil-water separator in stages; add the solution in the reaction bottle to a separatory funnel to separate to obtain 222.2 g of the lower liquid, and use acid-base titration to obtain the acid content For: 90.35% (mass fraction).
Embodiment 3
[0050] Embodiment 3: Preparation of high concentration hypophosphorous acid
[0051] Get 400.1g mass fraction to be 50% hypophosphorous acid and 250ml cyclohexane, add in the reaction bottle that oil-water separator and condenser are housed, fill up cyclohexane in oil-water separator;
[0052] Heat and stir under nitrogen protection until azeotropic for about 4 hours, discharge the water separated at the bottom of the oil-water separator in stages; add the solution in the reaction bottle to a separatory funnel to separate to obtain 212.4 g of the lower layer liquid, and use acid-base titration to obtain the acid content For: 94.07% (mass fraction).
[0053] Get the hypophosphorous acid 200.2g and 200ml methyl alcohol that the mass fraction is 94.07%, add in the reaction flask that oil-water separator and condenser are housed, and fixed solid calcium chloride is housed in oil-water separator and condenser wherein and in oil-water separation Fill the container with methanol, ...
PUM
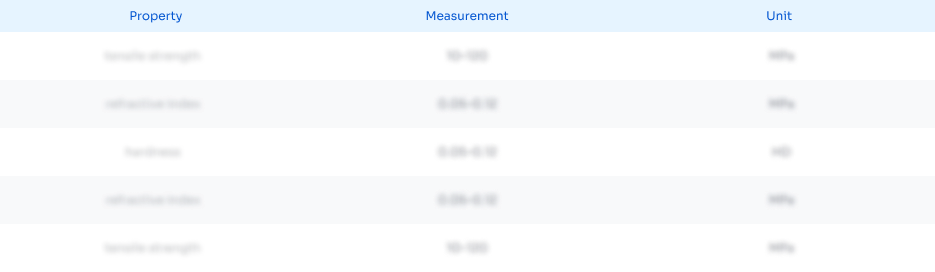
Abstract
Description
Claims
Application Information

- R&D Engineer
- R&D Manager
- IP Professional
- Industry Leading Data Capabilities
- Powerful AI technology
- Patent DNA Extraction
Browse by: Latest US Patents, China's latest patents, Technical Efficacy Thesaurus, Application Domain, Technology Topic.
© 2024 PatSnap. All rights reserved.Legal|Privacy policy|Modern Slavery Act Transparency Statement|Sitemap