Extrusion needle and extrusion method for large-specification thin-walled pipe or hollow profile
A technology for thin-walled pipes and hollow profiles, applied in metal extrusion, indenter/punch rods, metal processing equipment, etc., can solve the problems of increasing the cost of blanking and reaming, uneconomical production, and large reaming force , to achieve the effect of reducing the loss of drilling and boring metal and drilling tools, reducing production costs and improving production efficiency
- Summary
- Abstract
- Description
- Claims
- Application Information
AI Technical Summary
Problems solved by technology
Method used
Image
Examples
Embodiment Construction
[0017] The present invention will be further described below in conjunction with the accompanying drawings, but the present invention is not limited in any way. Any changes or improvements made based on the teaching of the present invention belong to the protection scope of the present invention.
[0018] Such as figure 1 As shown in the prior art, when generally hot-extruding large-scale thin-walled pipes or hollow profiles, larger holes need to be enlarged, and the enlarged holes are not in place at one time. It is necessary to cut and drill the holes on the drilling and boring machine first, and then pass through Reaming machine reaming, due to the large expansion coefficient of primary reaming, often need to carry out secondary reaming, at the same time, if image 3 As shown, since the extruding needle in the prior art mainly plays the role of piercing and fixing the inner diameter, in order to avoid scraping the glass lubricant in the inner hole of the billet when the ext...
PUM
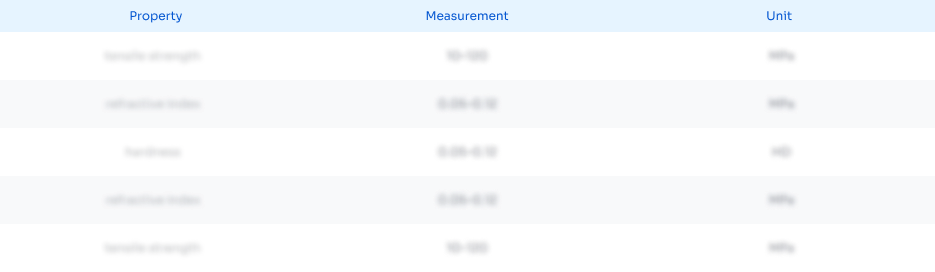
Abstract
Description
Claims
Application Information

- R&D
- Intellectual Property
- Life Sciences
- Materials
- Tech Scout
- Unparalleled Data Quality
- Higher Quality Content
- 60% Fewer Hallucinations
Browse by: Latest US Patents, China's latest patents, Technical Efficacy Thesaurus, Application Domain, Technology Topic, Popular Technical Reports.
© 2025 PatSnap. All rights reserved.Legal|Privacy policy|Modern Slavery Act Transparency Statement|Sitemap|About US| Contact US: help@patsnap.com