Flue gas desulfurization technology through additive enhanced coal slurry method
A desulfurization process and additive technology, applied in the field of flue gas purification, can solve the problems of high operating costs, slow leaching rate of coal-based pyrite, large liquid gas, etc., to increase leaching rate, increase mass transfer reaction rate, and improve leaching speed effect
- Summary
- Abstract
- Description
- Claims
- Application Information
AI Technical Summary
Problems solved by technology
Method used
Image
Examples
Embodiment 1
[0025] A coal-fired boiler with a rated evaporation capacity of 75t / h and a flue gas volume of 100,000 Nm 3 / h, SO 2 Content 1300mg / Nm 3 , flue gas temperature 135 ℃.
[0026] The absorption tower is a spray tower with a diameter of 4m and a height of 25m. The bottom of the absorption tower is used as a circulation pool. The operating liquid-gas ratio of the absorption tower is 6L / Nm 3 , the solid-liquid mass ratio of coal slurry is 2:10, the concentration of aluminum sulfate in the slurry (calculated as aluminum) is 200mg / L, the residence time of the slurry in the circulation tank is 10min, the desulfurization rate reaches 94%, and the coal slurry circulates for 10 hours The iron leaching rate is 15%.
Embodiment 2
[0028] A coal-fired boiler with a rated evaporation capacity of 75t / h and a flue gas volume of 100,000 Nm 3 / h, SO 2 Content 3300mg / Nm 3 , flue gas temperature 135 ℃.
[0029] The absorption tower is a spray tower with a diameter of 4m and a height of 25m. The bottom of the absorption tower is used as a circulation pool. The operating liquid-gas ratio of the absorption tower is 13L / Nm 3 , the solid-liquid mass ratio of coal slurry is 2:10, the concentration of aluminum ash in the slurry (calculated as aluminum) is 600mg / L, the residence time of the slurry in the circulation tank is 10min, the desulfurization rate reaches 98%, and the coal slurry circulates for 10 hours The iron leaching rate was 22%.
Embodiment 3
[0031] A coal-fired boiler with a rated evaporation capacity of 150t / h and a flue gas volume of 200,000 Nm 3 / h, SO 2 Content 1500mg / Nm 3 , flue gas temperature 125 ℃.
[0032] The absorption tower is a spray tower with a diameter of 5.5m and a height of 29m. The bottom of the absorption tower is used as a circulation pool. The operating liquid-gas ratio of the absorption tower is 8L / Nm 3 , the solid-liquid mass ratio of coal slurry is 2:10, the concentration of aluminum ash in the slurry (calculated as aluminum) is 300mg / L, the residence time of the slurry in the circulation tank is 10min, the desulfurization rate reaches 95%, and the coal slurry circulates for 10 hours The iron leaching rate reaches 16%.
PUM
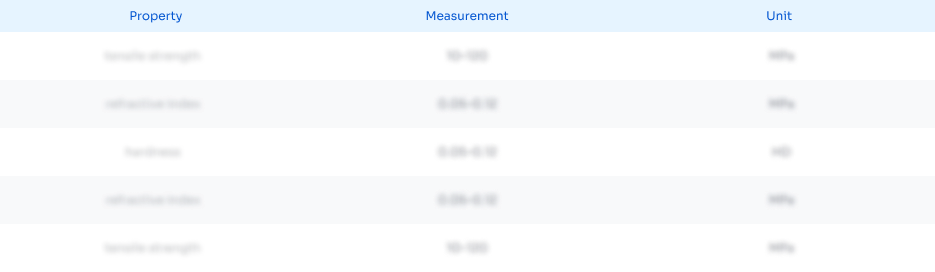
Abstract
Description
Claims
Application Information

- Generate Ideas
- Intellectual Property
- Life Sciences
- Materials
- Tech Scout
- Unparalleled Data Quality
- Higher Quality Content
- 60% Fewer Hallucinations
Browse by: Latest US Patents, China's latest patents, Technical Efficacy Thesaurus, Application Domain, Technology Topic, Popular Technical Reports.
© 2025 PatSnap. All rights reserved.Legal|Privacy policy|Modern Slavery Act Transparency Statement|Sitemap|About US| Contact US: help@patsnap.com