A kind of catalytic gasoline hydrodesulfurization method
A hydrodesulfurization and catalytic gasoline technology, which is applied in the fields of hydrotreating process, petroleum industry, hydrocarbon oil treatment, etc., can solve the problems of complex process flow and increased energy consumption of the device, and reduce investment and operation costs and energy consumption , Reduce equipment investment and operating costs
- Summary
- Abstract
- Description
- Claims
- Application Information
AI Technical Summary
Problems solved by technology
Method used
Image
Examples
Embodiment 1
[0036] Gasoline is pre-separated in the fractionation tower of the catalytic cracking unit to obtain light fractions and heavy fractions. The separation temperature of the light fractions and heavy fractions is 70°C; the light fractions are subjected to alkali extraction, and the products are used as clean gasoline blending components. It enters the pre-hydrogenation reactor and the selective hydrodesulfurization reactor successively. The prehydrogenation reaction conditions are: hydrogen partial pressure 1.8MPa, volume space velocity 3.8 h -1 , The reaction temperature is 178°C; the hydrodesulfurization reaction conditions are: hydrogen partial pressure 1.6MPa, volume space velocity 2.8h -1 , The reaction temperature is 282°C; the total hydrogen to oil volume ratio is 350:1.
[0037] It can be seen from Table 3 that using this technology can reduce the sulfur content of the product to below 10 μg / g, and the octane number of the product only loses 1.7 units.
Embodiment 2
[0039] Gasoline is pre-separated in the fractionation tower of the catalytic cracking unit to obtain light fractions and heavy fractions. The separation temperature of the light fractions and heavy fractions is 65°C; the light fractions are subjected to alkali extraction, and the products are used as clean gasoline blending components, and heavy fractions It enters the pre-hydrogenation reactor and the selective hydrodesulfurization reactor successively. The prehydrogenation reaction conditions are: hydrogen partial pressure 2.0MPa, volume space velocity 3.5 h -1 , The reaction temperature is 183°C; the hydrodesulfurization reaction conditions are: hydrogen partial pressure 1.8MPa, volume space velocity 3.0 h -1 , The reaction temperature is 288°C; the total hydrogen to oil volume ratio is 380:1.
[0040] It can be seen from Table 3 that using this technology can reduce the sulfur content of the product to below 10 μg / g, and the octane number of the product only loses 1.8 uni...
Embodiment 3
[0042] Gasoline is pre-separated in the fractionation tower of the catalytic cracking unit, and the separation temperature of the light fraction and the heavy fraction is 75°C; the light fraction is subjected to alkali extraction, and the product is used as a clean gasoline blending component, and the heavy fraction enters the pre-hydrogenation reactor successively and selective hydrodesulfurization reactors. The prehydrogenation reaction conditions are: hydrogen partial pressure 1.8MPa, volume space velocity 4.2 h -1 , Reaction temperature 180℃; hydrodesulfurization reaction conditions: hydrogen partial pressure 1.6MPa, volume space velocity 3.2 h -1 , The reaction temperature is 277°C; the total hydrogen to oil volume ratio is 320:1. The properties of raw oil and test results are listed in Table 2.
[0043] It can be seen from Table 3 that using this technology can reduce the sulfur content of the product to below 10 μg / g, and the octane number of the product will only los...
PUM
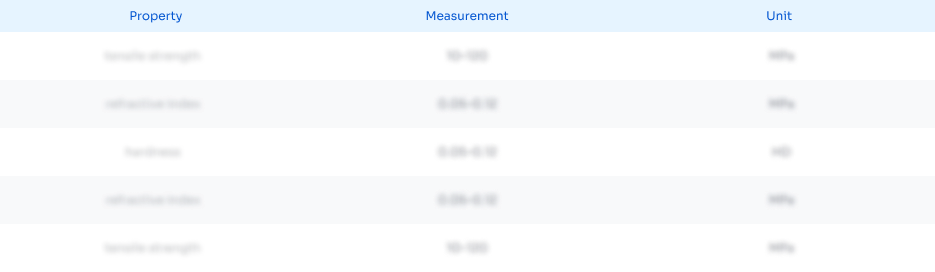
Abstract
Description
Claims
Application Information

- R&D
- Intellectual Property
- Life Sciences
- Materials
- Tech Scout
- Unparalleled Data Quality
- Higher Quality Content
- 60% Fewer Hallucinations
Browse by: Latest US Patents, China's latest patents, Technical Efficacy Thesaurus, Application Domain, Technology Topic, Popular Technical Reports.
© 2025 PatSnap. All rights reserved.Legal|Privacy policy|Modern Slavery Act Transparency Statement|Sitemap|About US| Contact US: help@patsnap.com