Control valve of carbon tank
A technology for controlling valves, carbon canisters, applied in the direction of valve details, valve devices, valve operation/release devices, etc.
- Summary
- Abstract
- Description
- Claims
- Application Information
AI Technical Summary
Problems solved by technology
Method used
Image
Examples
Embodiment Construction
[0022] see figure 1 and figure 2 , which is a specific embodiment of the carbon canister control valve of the present application. The carbon canister control valve includes an upper cover 10 and a housing 20, which are connected to each other by welding and kept sealed. There is a through hole 100 in the shape of a de Laval nozzle in the upper cover 10 . The cross-sectional area of the Laval tube first becomes smaller and then larger, and the gas passing through it can be accelerated. There are two pipelines under the housing 20 , the second pipeline on the right is a gas circulation pipeline, and the first pipeline on the left is used for installing the connector at the lower end of the pin 24 . There is a protrusion on the right side of the housing 20, which is a skeleton for placing rubber supports. The housing 20 has a magnetic tank 21, a coil bobbin 22, a coil 23, pins 24, a magnetic core 26, an armature 28 and Seat 29.
[0023] The magnetic pot 21 is roughly rin...
PUM
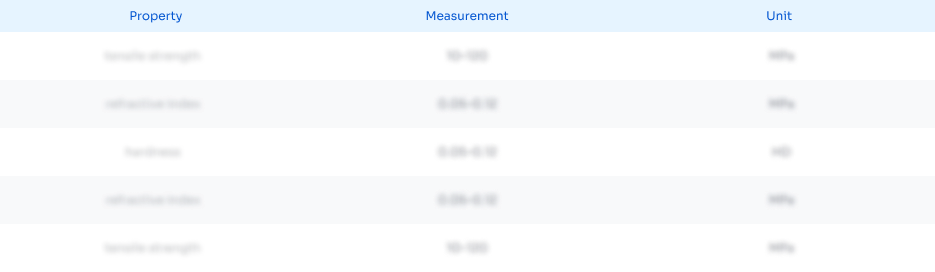
Abstract
Description
Claims
Application Information

- R&D
- Intellectual Property
- Life Sciences
- Materials
- Tech Scout
- Unparalleled Data Quality
- Higher Quality Content
- 60% Fewer Hallucinations
Browse by: Latest US Patents, China's latest patents, Technical Efficacy Thesaurus, Application Domain, Technology Topic, Popular Technical Reports.
© 2025 PatSnap. All rights reserved.Legal|Privacy policy|Modern Slavery Act Transparency Statement|Sitemap|About US| Contact US: help@patsnap.com