Burnt-out processing technology of polar fleece fabric
A processing technology, polar fleece technology, applied in dyeing, textiles and papermaking, etc., can solve problems such as non-color registration, single fabric design form, safety problems, etc., to solve safety problems and damage to mechanical appliances , Light color fastness has no adverse effects, and the effect of overcoming poor color development
- Summary
- Abstract
- Description
- Claims
- Application Information
AI Technical Summary
Problems solved by technology
Method used
Image
Examples
Embodiment 1
[0018] A burn-out processing technology for polar fleece fabrics, which uses printing paste to perform burn-out printing on the polar fleece surface of a light base according to a designed pattern, and the processing process is printing→drying→fixing→washing→soap Washing → washing → dehydration → shaping → packaging, the printing paste includes 45% by mass of etchant, 44% by mass of disperse printing paste, 6% by mass of disperse dye, and the rest is water; The screen processing is carried out, the pressure of the magnetic bar is 35% during printing, and the speed is 15 m / min; the drying temperature is 110°C; the color is fixed at 145°C x 6min; the following specific processes are included in the order of washing→soaping→water washing: washing with water for 10min → Wash with hot water at 40°C and anti-contamination agent for 18 minutes → Reduction washing: hydrosulfite 3g / L, caustic soda 3g / L, soaping agent concentration 2%, temperature 80°C, wash for 10 minutes → wash with wa...
Embodiment 2
[0020] A burn-out processing technology for polar fleece fabrics, which uses printing paste to perform burn-out printing on the polar fleece surface of a light base according to a designed pattern, and the processing process is printing→drying→fixing→washing→soap Washing→Washing→Dehydration→Styling→Packaging, the printing paste includes 50% by mass of etchant, 40% by mass of disperse printing paste, 8% by mass of disperse dye, and the rest is water; burnt-out printing According to the ordinary flat screen printing process, the pressure of the magnetic bar is 25% during printing, and the speed is 35m / min; the drying temperature is 120°C; the color is fixed at 140°C x 7min; the following specific processes are included in the order of washing→soaping→water washing: water Wash for 25 minutes → wash with 60°C hot water and anti-contamination agent for 10 minutes → reduce washing: hydrosulfite 2g / L, caustic soda 4g / L, soaping agent concentration 1.5%, temperature 90°C, wash for 18 m...
Embodiment 3
[0022] A burn-out processing technology for polar fleece fabrics, which uses printing paste to perform burn-out printing on the polar fleece surface of a light base according to a designed pattern, and the processing process is printing→drying→fixing→washing→soap Washing→Washing→Dehydration→Styling→Packaging, the printing paste includes 55% by mass of etchant, 42% by mass of disperse printing paste, 2% by mass of disperse dyes, and the rest is water; burnt-out printing according to Ordinary rotary screen processing is carried out, the pressure of the magnetic bar is 30% during printing, and the speed of the vehicle is 25m / min; the drying temperature is 130°C; the color is fixed at 150°C x 2min; the following specific processes are included in the order of washing→soaping→water washing: washing with water 18 min→wash with 80℃ hot water and anti-contamination agent for 25min→reduction washing: hydrosulfite 4g / L, caustic soda 2g / L, soaping agent concentration 2.5%, temperature 100...
PUM
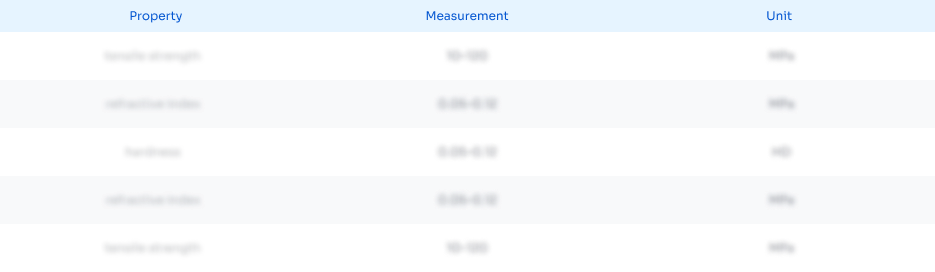
Abstract
Description
Claims
Application Information

- Generate Ideas
- Intellectual Property
- Life Sciences
- Materials
- Tech Scout
- Unparalleled Data Quality
- Higher Quality Content
- 60% Fewer Hallucinations
Browse by: Latest US Patents, China's latest patents, Technical Efficacy Thesaurus, Application Domain, Technology Topic, Popular Technical Reports.
© 2025 PatSnap. All rights reserved.Legal|Privacy policy|Modern Slavery Act Transparency Statement|Sitemap|About US| Contact US: help@patsnap.com