Method for smelting vanadium iron
A technology of vanadium oxide and iron oxide, applied in the field of smelting ferrovanadium, can solve the problems of low recovery rate of vanadium and the like
- Summary
- Abstract
- Description
- Claims
- Application Information
AI Technical Summary
Problems solved by technology
Method used
Examples
Embodiment 1
[0039] This example is used to illustrate the method provided by the present invention.
[0040] Vanadium pentoxide, unslaked lime (CaO content is 85% by weight, the same below), iron and aluminum are mixed to obtain charge, wherein, relative to the oxygen element per mole in the vanadium pentoxide, the consumption of aluminum is 0.804 moles, The weight ratio of quicklime and aluminum is 1: 1.85; Relative to 1 weight part of iron, the consumption of vanadium pentoxide is 4 parts by weight in terms of vanadium element; that is, the weight ratio of vanadium pentoxide, aluminum, quicklime and iron It is 36.4:21.708:11.73:5.1.
[0041] After loading 2.93 tons of the above charge into a tilting electric arc furnace with a nominal capacity of 20 tons, heat the above charge to 1850°C within 15 minutes after powering on, and maintain it within the temperature range of 1850-1950°C for 30 minutes, and then according to GB / According to the ferrous ammonium sulfate titration method spec...
Embodiment 2
[0044] This example is used to illustrate the method provided by the present invention.
[0045] Mix vanadium pentoxide, quicklime, iron and aluminum uniformly to obtain charge, wherein, relative to every mole of oxygen in vanadium pentoxide, the amount of aluminum is 0.824 moles, and the weight ratio of quicklime to aluminum is 1:2; Relative to 1 part by weight of iron, the amount of vanadium pentoxide used is 4 parts by weight in terms of vanadium element; that is, the weight ratio of vanadium pentoxide, aluminum, quicklime and iron is 36.4:22.248:11.124:5.1.
[0046] After loading 2.94 tons of the above charge into a tilting electric arc furnace with a nominal capacity of 20 tons, heat the above charge to 1820°C within 15 minutes of power on, and maintain it within the temperature range of 1820-1900°C for 32 minutes, and then according to GB / According to the method specified in the ferrous ammonium sulfate titration method specified in T 8704.5-2007, the total vanadium con...
Embodiment 3
[0049] This example is used to illustrate the method provided by the present invention.
[0050] Mix vanadium pentoxide, quicklime, iron and aluminum uniformly to obtain charge, wherein, relative to every mole of oxygen in vanadium pentoxide, the amount of aluminum is 0.838 moles, and the weight ratio of quicklime to aluminum is 1:1.7; Relative to 1 part by weight of iron, the amount of vanadium pentoxide used is 4 parts by weight in terms of vanadium element; that is, the weight ratio of vanadium pentoxide, aluminum, quicklime and iron is 36.4:22.626:13.31:5.1.
[0051] After loading 3.04 tons of the above-mentioned charge into a tilting electric arc furnace with a nominal capacity of 20 tons, heat the above-mentioned charge to 1900°C within 20 minutes after powering on, and maintain it in the temperature range of 1900-2000°C for 25 minutes, and then according to GB / According to the ferrous ammonium sulfate titration method specified in T 8704.5-2007, it is measured that the...
PUM
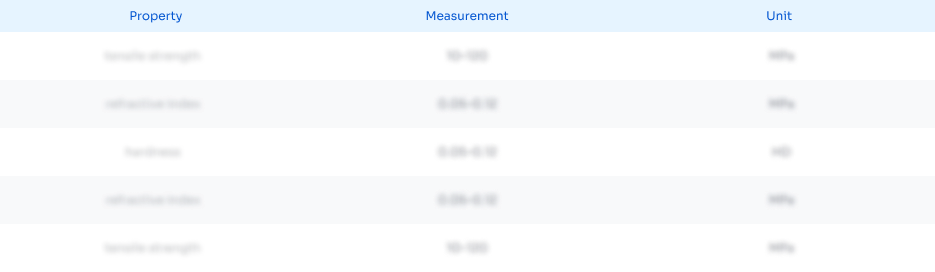
Abstract
Description
Claims
Application Information

- Generate Ideas
- Intellectual Property
- Life Sciences
- Materials
- Tech Scout
- Unparalleled Data Quality
- Higher Quality Content
- 60% Fewer Hallucinations
Browse by: Latest US Patents, China's latest patents, Technical Efficacy Thesaurus, Application Domain, Technology Topic, Popular Technical Reports.
© 2025 PatSnap. All rights reserved.Legal|Privacy policy|Modern Slavery Act Transparency Statement|Sitemap|About US| Contact US: help@patsnap.com