Modified plastic, and making method and use thereof
A plastic modification technology, which is applied in the field of polymer modification technology and processing, can solve the problems of complex processing, high production cost, product strength and impact degradation, etc., and achieve good flame retardancy, low production cost, Ease of processing
- Summary
- Abstract
- Description
- Claims
- Application Information
AI Technical Summary
Problems solved by technology
Method used
Image
Examples
Embodiment 1
[0039] (1) Add 52 parts of talcum powder, 35 parts of calcium carbonate, 45 parts of glass fiber, 100 parts of polyethylene resin (LLDPE:HDPE=1.5:3), and 95 parts of waste polyvinyl chloride into the high-speed mixer according to the proportion of the formula. Stir for 35min, then add 10 parts of tris(1,2,2,6,6-pentamethylpiperidine) phosphite, composite antioxidant (6 parts of antioxidant CA and 10105 parts of antioxidant), o- 18 parts of dioctyl phthalate, inorganic composite flame retardant (50 parts of aluminum hydroxide and 20 parts of antimony trioxide), 1.8 parts of polyethylene wax, continue to mix and stir for 5 minutes, and the speed is 760r / min;
[0040] (2) Mix the above-mentioned materials with a roller press for 8 minutes, and the mixing temperature is 110-120°C;
[0041] (3) Place the above-mentioned kneaded material in an extruder to extrude and granulate, the temperature is controlled at 145°C, and the screw speed is 28r / min;
[0042] (4) Injection molding th...
Embodiment 2
[0045] (1) Add 65 parts of kaolin, 48 parts of calcium carbonate, 60 parts of carbon fiber, 100 parts of polyethylene resin (LLDPE:HDPE=2:3), and 80 parts of waste polyethylene into the high-speed mixer according to the proportion of the formula and mix them for 35 minutes. Then add 12 parts of 2-hydroxy-4-n-octyloxybenzophenone, compound antioxidant (8 parts of antioxidant DLTP and 10106 parts of antioxidant), 15 parts of dinonyl phthalate, inorganic Composite flame retardant (35 parts of aluminum hydroxide and 16 parts of antimony trioxide), 1.5 parts of polyethylene wax, continue to mix and stir for 6 minutes, and the speed is 840r / min;
[0046] (2) Mix the above-mentioned materials with a roller press for 10 minutes, and the mixing temperature is 120-130°C;
[0047] (3) Place the above-mentioned kneaded material in an extruder to extrude and granulate, the temperature is controlled at 130°C, and the screw speed is 25r / min;
[0048] (4) Injection molding the above pellets,...
Embodiment 3
[0051](1) Add 40 parts of kaolin, 22 parts of calcium carbonate, 30 parts of carbon fiber, 100 parts of polyethylene resin (LLDPE:HDPE=1:3), and 135 parts of waste polyethylene into the high-speed mixer according to the formula ratio and mix for 35 minutes. Then add 8 parts of tris(1,2,2,6,6-pentamethylpiperidine) phosphite, composite antioxidant (6 parts of antioxidant CA and 6 parts of antioxidant DLTP), phthalate 20 parts of dioctyl formate, inorganic composite flame retardant (52 parts of aluminum hydroxide and 23 parts of antimony trioxide), 1.8 parts of polyethylene wax, continue to mix and stir for 10 minutes, and the speed is 540r / min;
[0052] (2) Mix the above-mentioned materials with a roller press for 10 minutes, and the mixing temperature is 120-130°C;
[0053] (3) Place the above-mentioned kneaded material in an extruder to extrude and granulate, the temperature is controlled at 150°C, and the screw speed is 30r / min;
[0054] (4) Injection molding the above pell...
PUM
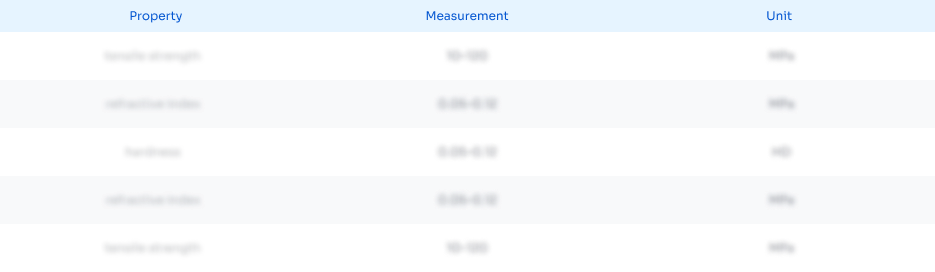
Abstract
Description
Claims
Application Information

- R&D
- Intellectual Property
- Life Sciences
- Materials
- Tech Scout
- Unparalleled Data Quality
- Higher Quality Content
- 60% Fewer Hallucinations
Browse by: Latest US Patents, China's latest patents, Technical Efficacy Thesaurus, Application Domain, Technology Topic, Popular Technical Reports.
© 2025 PatSnap. All rights reserved.Legal|Privacy policy|Modern Slavery Act Transparency Statement|Sitemap|About US| Contact US: help@patsnap.com