Epoxy modified saturated polyester resin for undercoat of coil coating and undercoat of coil coating
A coil coating and epoxy modification technology, applied in the direction of anti-corrosion coatings, polyester coatings, coatings, etc., can solve the problems of weak deformation and weather resistance, little performance improvement, and poor miscibility, etc., to achieve comprehensive Effect of performance improvement, strong adhesion and corrosion resistance, good surface hardness and weather resistance
- Summary
- Abstract
- Description
- Claims
- Application Information
AI Technical Summary
Problems solved by technology
Method used
Image
Examples
Embodiment 1
[0029] Example 1 Preparation of Epoxy Modified Saturated Polyester Resin
[0030] By weight, the content of each component in the epoxy modified saturated polyester resin is:
[0031]
[0032] Formula construction process: Put methyl propylene glycol, epoxy resin 609, isophthalic acid, adipic acid, neopentyl glycol and dibutyltin dilaurate into the reaction kettle in proportion, raise the temperature to 130°C, start stirring, React at ℃ for 2 hours, slowly raise the temperature to 180℃, keep it for 1 hour, continue to raise the temperature to 200℃ for continuous esterification reaction until the resin is transparent, cool down to below 180℃, add xylene, heat up to xylene reflux (200℃~220℃ ), reflux reaction until the acid value of the resin is ≤5 mgKOH, lower the temperature to below 180°C, add S-150# and propylene glycol methyl ether in proportion to dilute, stir evenly, filter, discharge, and pack.
Embodiment 2
[0033] Example 2 Preparation of Epoxy-modified Saturated Polyester Resin
[0034] By weight, the content of each component in the epoxy modified saturated polyester resin is:
[0035]
[0036]
[0037] Formula construction process: Put methyl propylene glycol, epoxy resin 609, isophthalic acid, adipic acid, neopentyl glycol and dibutyl tin oxide into the reaction kettle in proportion, raise the temperature to 135°C, start stirring, and react at 148°C For 2 hours, slowly raise the temperature to 180°C, keep it for 1 hour, continue to heat up to 205°C for continuous esterification reaction until the resin is transparent, cool down to below 180°C, add xylene, heat up to xylene reflux, and reflux reaction until the acid value of the resin is ≤ 5 mgKOH, lower the temperature to below 180°C, add S-150# and propylene glycol methyl ether in proportion to dilute, stir evenly, filter, discharge, and pack.
Embodiment 3
[0038] Example 3 Preparation of Epoxy-modified Saturated Polyester Resin
[0039] By weight, the content of each component in the epoxy modified saturated polyester resin is:
[0040]
[0041] Formula construction process: Put methyl propylene glycol, epoxy resin 609, isophthalic acid, adipic acid, neopentyl glycol and monobutyl tin oxide into the reaction kettle in proportion, raise the temperature to 128°C, start stirring, and react at 145°C After 2.5 hours, slowly raise the temperature to 180°C, keep it for 1 hour, continue to heat up to 205°C for continuous esterification reaction until the resin is transparent, cool down to below 180°C, add xylene, heat up to xylene reflux, and reflux until the acid value of the resin is ≤ 5 mgKOH, lower the temperature below 180°C, add S-150# and propylene glycol methyl ether in proportion to dilute, stir evenly, filter, discharge, and pack.
PUM
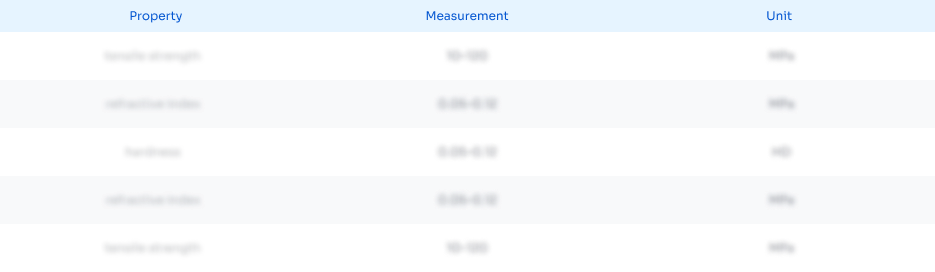
Abstract
Description
Claims
Application Information

- R&D
- Intellectual Property
- Life Sciences
- Materials
- Tech Scout
- Unparalleled Data Quality
- Higher Quality Content
- 60% Fewer Hallucinations
Browse by: Latest US Patents, China's latest patents, Technical Efficacy Thesaurus, Application Domain, Technology Topic, Popular Technical Reports.
© 2025 PatSnap. All rights reserved.Legal|Privacy policy|Modern Slavery Act Transparency Statement|Sitemap|About US| Contact US: help@patsnap.com