Method for preparing epoxidized fatty acid methyl ester with microreactor one-step method
A technology of epoxy fatty acid methyl ester and microreactor, applied in the direction of organic chemistry and the like, can solve the problems of inability to prepare epoxy fatty acid methyl ester, inability to accurately control temperature, incapable of continuous production, etc., and achieve short reaction residence time and production equipment. Simple, easy-to-operate controls
- Summary
- Abstract
- Description
- Claims
- Application Information
AI Technical Summary
Problems solved by technology
Method used
Image
Examples
Embodiment 1
[0038] Soybean oil (first raw material storage tank 1) and methanol solution of sodium methoxide (wherein sodium methoxide accounts for 1wt% of soybean oil (second raw material storage tank 2) are passed through the second raw material sequentially according to the molar ratio of soybean oil and methanol as 1:13 A microstructure mixer 3, a first heat exchanger 4, a first tubular temperature control module 5, and a first microstructure reactor 6, and react in the first microstructure reactor 6 at normal pressure and 75° C. for 7 minutes At the same time, the mixture of 30wt% hydrogen peroxide, 98wt% formic acid, 98wt% concentrated sulfuric acid and EDTA (the third raw material storage tank 7) is injected into the first microstructure reactor 6 through another constant flow pump. Two microstructure mixers 8, wherein the molar ratio of hydrogen peroxide and formic acid is 1:1, the added quality of concentrated sulfuric acid is 3% of the soybean oil quality, the added quality of ED...
Embodiment 2
[0040] Soybean oil (first raw material storage tank 1) and methanol solution of sodium methoxide (wherein sodium methoxide accounts for 1wt% of soybean oil (second raw material storage tank 2) pass through the first The microstructure mixer 3 , the first heat exchanger 4 , the first tubular temperature control module 5 and the first microstructure reactor 6 are reacted in the first microstructure reactor 6 at normal pressure and 75° C. for 7 minutes. At the same time, the mixture of 30wt% hydrogen peroxide, 98wt% formic acid, 98wt% concentrated sulfuric acid and urea (the third raw material storage tank 7) is fed into the second Microstructure mixer 8, wherein the molar ratio of hydrogen peroxide and formic acid is 1:1, the added mass of concentrated sulfuric acid is 4% of the mass of soybean oil, the mass of urea added is 3% of the mass of soybean oil, and the formic acid and soybean oil are guaranteed The molar ratio of the number of double bonds is 14:1, and the material pa...
Embodiment 3-8
[0042] Adopt the reaction condition identical with embodiment 1, difference is, embodiment 3-4 replaces soybean oil with cottonseed oil; Embodiment 5-6 replaces soybean oil with peanut oil, replaces formic acid with acetic acid simultaneously; Embodiment 7-8 uses Rapeseed oil was substituted for soybean oil; the epoxy fatty acid methyl ester product was obtained, and its epoxy value is shown in Table 1.
[0043] Table 1
[0044] Example number
[0045] 8
PUM
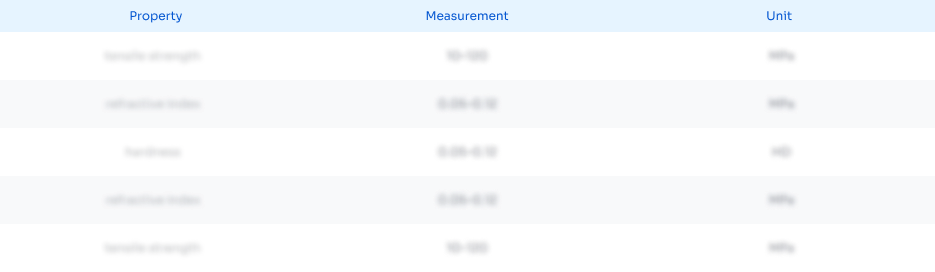
Abstract
Description
Claims
Application Information

- Generate Ideas
- Intellectual Property
- Life Sciences
- Materials
- Tech Scout
- Unparalleled Data Quality
- Higher Quality Content
- 60% Fewer Hallucinations
Browse by: Latest US Patents, China's latest patents, Technical Efficacy Thesaurus, Application Domain, Technology Topic, Popular Technical Reports.
© 2025 PatSnap. All rights reserved.Legal|Privacy policy|Modern Slavery Act Transparency Statement|Sitemap|About US| Contact US: help@patsnap.com