Method and device for continuously preparing glutaraldehyde
A technology for glutaraldehyde and dihydropyran, applied in the field of continuous production of glutaraldehyde, high-purity glutaraldehyde continuous production method and production equipment, can solve the problems of slow reaction speed, high impurity content, and many by-products , to achieve the effect of no stirring energy consumption, simple equipment structure and mild reaction conditions
- Summary
- Abstract
- Description
- Claims
- Application Information
AI Technical Summary
Problems solved by technology
Method used
Image
Examples
Embodiment 1
[0033] The static mixer that the embodiment of the present invention adopts is SV-3.5 / 32 type, and the tubular reactor volume is 0.2m 3 , the diameter of the rectification tower is Φ600, and the filling specification of the rectification tower is Dn25 SO 4 2- / TiO 2 -AL 2 o 3 -Al solid acid Raschig ring catalytic rectification filler 9m (this filler is equivalent to 2~2.5 theoretical plates per meter), of which, the rectification section is 5m, and the stripping section is 4m.
[0034] First, feed 2-methoxy-3,4-dihydropyran 800kg / h, water 960kg / h and phosphoric acid 0.5kg / h into the static mixer; In a tubular reactor, it is hydrolyzed at 95°C and 1.0Mpa (the residence time is about 6 minutes based on the feed volume and the volume of the tubular reactor). The hydrolysis conversion of 2-methoxy-3,4-dihydropyran after partial hydrolysis was 86%.
[0035] Secondly, the hydrolyzate after partial hydrolysis in the tubular reactor is passed into the rectification tower, and th...
Embodiment 2
[0039] First of all, this embodiment adopts the device in Embodiment 1 and the production process is the same, 600 kg / h of 2-methoxy-3,4-dihydropyran, 760 kg / h of water and 0.35 kg of phosphoric acid are introduced into the static mixer / h. In a tubular reactor, hydrolyze at 80°C and 0.3Mpa (the residence time is about 9 minutes according to the volume of the feed and the volume of the tubular reactor), after partial hydrolysis, 2-methoxy-3,4- The hydrolysis conversion rate of dihydropyran was 89%.
[0040] Secondly, in the reactive distillation process, the reactive distillation conditions are as follows: the pressure at the top of the tower is 46KPa, the temperature at the bottom of the tower is 86°C, and the reflux ratio is 0.7.
[0041] Finally, 349.9kg / h distillate was obtained from the top of the tower, among which, methanol 165.7kg / h, glutaraldehyde 6kg / h, 2-methoxy-3,4-dihydropyran 2.5kg / h and water 167.7 kg / h. Obtain glutaraldehyde finished product from the bottom ...
Embodiment 3
[0044] The static mixer that the embodiment of the present invention adopts is SV-2.3 / 20 type, and the tubular reactor volume is 0.15m 3 , the diameter of the rectification tower is Φ450, the packing is bagged β-zeolite 16m (each meter of this packing is equivalent to 1 theoretical plate), among them, the rectification section is 10m, and the stripping section is 6m.
[0045] First, feed 2-methoxy-3,4-dihydropyran 300kg / h, water 400kg / h and phosphoric acid 0.2kg / h into the static mixer; In a type reactor, it is hydrolyzed at 75°C and 0.2Mpa (the residence time is about 13 minutes based on the feed volume and the volume of the tubular reactor). The hydrolysis conversion rate of 2-methoxy-3,4-dihydropyran after partial hydrolysis was 90%.
[0046] Secondly, the hydrolyzate after partial hydrolysis in the tubular reactor is passed into the rectification tower, and the reaction rectification conditions are as follows: the pressure at the top of the tower is 33KPa, the temperature...
PUM
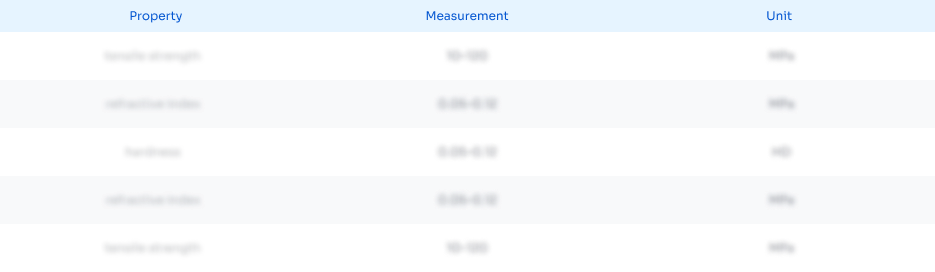
Abstract
Description
Claims
Application Information

- Generate Ideas
- Intellectual Property
- Life Sciences
- Materials
- Tech Scout
- Unparalleled Data Quality
- Higher Quality Content
- 60% Fewer Hallucinations
Browse by: Latest US Patents, China's latest patents, Technical Efficacy Thesaurus, Application Domain, Technology Topic, Popular Technical Reports.
© 2025 PatSnap. All rights reserved.Legal|Privacy policy|Modern Slavery Act Transparency Statement|Sitemap|About US| Contact US: help@patsnap.com