Method for preparing feed grade calcium hydrophosphate by phosphorite decomposition by hydrochloric acid
A calcium hydrogen phosphate, feed-grade technology, applied in chemical instruments and methods, phosphorus compounds, inorganic chemistry, etc., can solve the problems of unstable product quality of calcium hydrogen phosphate, unfavorable environmental protection of phosphogypsum, high production cost, etc., to alleviate sulfur resources The effect of tension, low cost and short production process
- Summary
- Abstract
- Description
- Claims
- Application Information
AI Technical Summary
Problems solved by technology
Method used
Image
Examples
Embodiment 1
[0039] Will P 2 o 5 The phosphate rock with a content of 17% was crushed to 200 mesh, and 1300g of hydrochloric acid with a mass concentration of 20% was added, and reacted for 50 minutes; the temperature was raised to 55°C, and Na 2 S 0.5g, H 2 o 2 0.2g, reacted for 30min, filtered; added 250g of melamine to the filtrate, reacted for 30min, passed through 280g of ammonia water with a mass concentration of 20%, reacted for 40min, filtered; the filtrate was adjusted to pH 6.5 with calcium hydroxide solution, stirred for 20min, filtered and baked Dried calcium hydrogen phosphate 123g, through analysis quality reaches feed grade calcium hydrogen phosphate first-class product requirement.
Embodiment 2
[0041] Will P 2 o 5 The phosphate rock with a content of 17% was crushed to 100 mesh, and 1200g of hydrochloric acid with a mass concentration of 25% was added to react for 40 minutes; the temperature was raised to 60°C, and Na 2 S 0.7g, H 2 o 2 0.4g, reacted for 35min, filtered; added 280g of melamine to the filtrate, reacted for 45min, passed through 260g of ammonia water with a mass concentration of 25%, reacted for 40min, filtered; the filtrate was adjusted to pH 7 with calcium hydroxide solution, stirred for 35min, filtered and baked Dried calcium hydrogen phosphate 135g, through analysis quality reaches feed grade calcium hydrogen phosphate first-class product requirement.
Embodiment 3
[0043] Will P 2 o 5 The phosphate rock with a content of 17% was crushed to 80 mesh, and 1200g of hydrochloric acid with a mass concentration of 25% was added, and reacted for 40 minutes; the temperature was raised to 60°C, and Na 2 S 0.7g, activated carbon 0.4g, react for 35min, filter; add 280g of melamine to the filtrate, react for 45min, pass through 260g of ammonia water with a mass concentration of 25%, react for 40min, filter; adjust the pH value of the filtrate to 7 with calcium hydroxide solution, stir for 35min , filtered and dried to obtain 135g of dibasic calcium phosphate, which reached the requirements of first-class feed grade dibasic calcium phosphate through analysis.
PUM
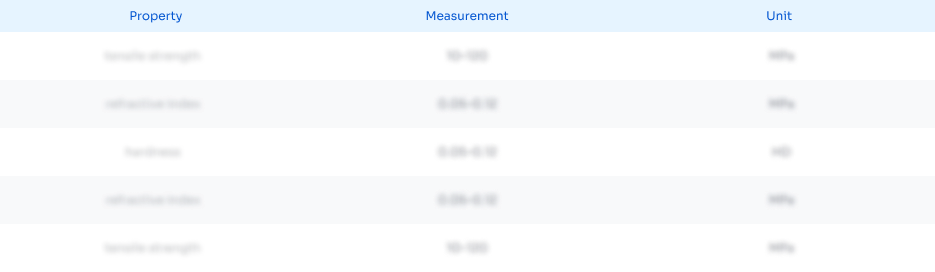
Abstract
Description
Claims
Application Information

- R&D Engineer
- R&D Manager
- IP Professional
- Industry Leading Data Capabilities
- Powerful AI technology
- Patent DNA Extraction
Browse by: Latest US Patents, China's latest patents, Technical Efficacy Thesaurus, Application Domain, Technology Topic, Popular Technical Reports.
© 2024 PatSnap. All rights reserved.Legal|Privacy policy|Modern Slavery Act Transparency Statement|Sitemap|About US| Contact US: help@patsnap.com