Electro-plastic friction stir spot welding device and method thereof
A technology of friction stir and electroplasticity, which is applied in the direction of non-electric welding equipment, welding equipment, metal processing equipment, etc., can solve the problems of weak connection surface, low interface temperature, virtual connection and holes, etc., to strengthen the inherently weak connection surface, Effects of improving forming temperature and environment and improving plastic flow ability
- Summary
- Abstract
- Description
- Claims
- Application Information
AI Technical Summary
Problems solved by technology
Method used
Image
Examples
Embodiment Construction
[0019] Hereinafter, preferred embodiments of the present invention are given in conjunction with the drawings to illustrate the technical solutions of the present invention in detail.
[0020] Such as figure 1 As shown, an electroplastic friction stir spot welding device of the present invention includes a stirring sleeve 2, a stirring needle 1 in the stirring sleeve, a clamping sleeve 3 clamped outside the stirring sleeve 2, and a welding pad 4 There is a welding workpiece between the clamping sleeve 3 and the welding pad 4, characterized in that the bottom of the clamping sleeve 3 and the top of the welding pad 4 are respectively provided with two radial opening grooves, and The brush 5 is installed in the groove, and the shape of the groove matches the shape of the conductive block in the brush 5.
[0021] Preferably, the clamping sleeve 3 and the welding pad 4 are made of insulating materials, or the surfaces are coated with insulating paint.
[0022] Such as figure 2 As shown...
PUM
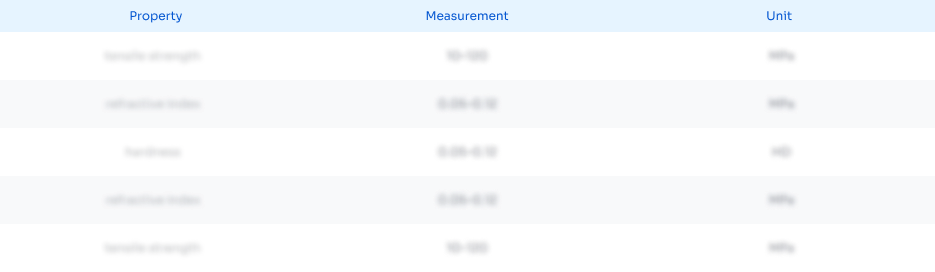
Abstract
Description
Claims
Application Information

- R&D Engineer
- R&D Manager
- IP Professional
- Industry Leading Data Capabilities
- Powerful AI technology
- Patent DNA Extraction
Browse by: Latest US Patents, China's latest patents, Technical Efficacy Thesaurus, Application Domain, Technology Topic, Popular Technical Reports.
© 2024 PatSnap. All rights reserved.Legal|Privacy policy|Modern Slavery Act Transparency Statement|Sitemap|About US| Contact US: help@patsnap.com