New method for synthesizing nanometal particle-loaded carbon nanofiber
A technology of nano metal particles and carbon nanofibers
- Summary
- Abstract
- Description
- Claims
- Application Information
AI Technical Summary
Problems solved by technology
Method used
Image
Examples
Embodiment 1
[0027] In the first step, weigh 2.0g of polyvinylpyrrolidone and 0.9g of ferrocene and dissolve them in a beaker, add 11ml of absolute ethanol and 9ml of dimethylformamide solvent, and place them in the beaker with magnetic stirring to form a uniform orange solution.
[0028] The second step is to transfer the prepared solution into the syringe, connect the electrospinning device, and set the spinning conditions, the voltage is 13Kv, the injection rate is 1ml / h, and the receiving distance is 15cm. The high-pressure generator was started, and the spinning process lasted for 5 hours, and then the prepared composite nanofibers were dried at 60 °C. Use tweezers to peel off the early composite product from the aluminum foil, and use a field emission scanning electron microscope (Philips, XL-30E, SEM) with a scanning voltage of 3KV and a magnification of 60,000 times ( figure 1 ) conditions, it can be seen that the early composite product has a one-dimensional linear structure, but ...
Embodiment 2
[0035] In the first step, weigh 1.0 g of polyacrylonitrile and 0.5 g of ferrocene and dissolve them in a beaker, add 10 ml of dimethylformamide solvent, and stir magnetically to form a uniform orange solution.
[0036] The second step is to transfer the prepared solution into the syringe, connect the electrospinning device, and set the spinning conditions, the voltage is 10Kv, the injection rate is 0.5ml / h, and the receiving distance is 19cm. Start the high-voltage generator, and the spinning process lasts for 5 hours, and then the prepared composite nanofibers are dried at 61 ° C. The product and the aluminum foil are peeled off with tweezers.
[0037] In the third step, the product of the second step is transferred to a tube furnace, heated to 250°C at a rate of 2°C / min in an air atmosphere, and kept at this temperature for 0.5h. Then in an argon atmosphere Continue heating to 700°C, keep warm for 1h, then cool down to room temperature naturally. The product obtained at thi...
Embodiment 3
[0041] In the first step, weigh 1.5g of polyvinylpyrrolidone and 0.6g of ferrocene and dissolve them in a beaker, add 9ml of absolute ethanol and 6ml of dimethylformamide solvent, and place them in the beaker with magnetic stirring to form a uniform orange solution.
[0042] The second step is to transfer the prepared solution into the syringe, connect the electrospinning device, and set the spinning conditions, the voltage is 11Kv, the injection rate is 0.6ml / h, and the receiving distance is 17cm. Start the high-voltage generator, and the spinning process lasts for 10 hours, and then the prepared composite nanofibers are dried at 64°C. The product and the aluminum foil are peeled off with tweezers.
[0043] In the third step, the product of the second step is transferred to a tube furnace, directly heated to 600°C at a rate of 1°C / min in an argon atmosphere, kept at this temperature for 2h, and then naturally cooled to room temperature. The product obtained at this time is th...
PUM
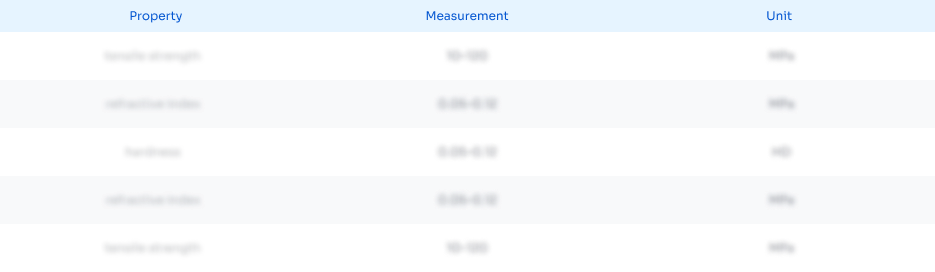
Abstract
Description
Claims
Application Information

- R&D
- Intellectual Property
- Life Sciences
- Materials
- Tech Scout
- Unparalleled Data Quality
- Higher Quality Content
- 60% Fewer Hallucinations
Browse by: Latest US Patents, China's latest patents, Technical Efficacy Thesaurus, Application Domain, Technology Topic, Popular Technical Reports.
© 2025 PatSnap. All rights reserved.Legal|Privacy policy|Modern Slavery Act Transparency Statement|Sitemap|About US| Contact US: help@patsnap.com