Preparation method of energy-storage light-emitting concrete
A technology of energy storage and luminescence, concrete, applied in the direction of luminescent materials, chemical instruments and methods, etc.
- Summary
- Abstract
- Description
- Claims
- Application Information
AI Technical Summary
Problems solved by technology
Method used
Examples
Embodiment 1
[0018] (a) CaO:xDy 3+ , yNa + Preparation of phosphor powder: CaCO 3 , Na 2 CO 3 (both are analytically pure) and Dy 2 o 3 (99.99%, analytically pure) weighed accurately according to the molar ratio Ca:Dy:Na=l:0.01:0.1, added a small amount of ethanol (as a grinding aid), fully ground evenly, and dried in an oven at 110°C for 3 hours. The precursor was obtained, calcined at 950°C for 2 hours, cooled, and ground to obtain white powdery phosphor; (b) Preparation of luminous concrete: according to the mass percentage of each component, phosphor powder 4%, white cement 18%, standard sand 27%, stone 43%, water 8% and accurately weigh various substances; clean the weighed gravel and dry it, put the dried gravel, cement, standard sand, water and fluorescent powder together Stir in the blender, after stirring evenly, put the mixture into the mold, remove the mold after 24 hours, and then put the test block into the standard curing box for curing.
Embodiment 2
[0020] (a) CaO:xDy 3+ , yNa + Preparation of phosphor powder: CaCO 3 , Na 2 CO 3 (both are analytically pure) and Dy 2 o 3 (99.99%, analytically pure) according to the molar ratio Ca:Dy:Na=l:0.015:0.2, accurately weighed, added a small amount of ethanol (as a grinding aid), fully ground evenly, and dried in an oven at 110°C for 3 hours. The precursor was obtained, calcined at 1050°C for 2.5h, cooled, and ground to obtain white powdery phosphor; (b) Preparation of luminous concrete: according to the mass percentage of each component, phosphor powder 6%, white cement 18%, standard 27% of sand, 41% of stone, and 8% of water are used to accurately weigh various substances; clean and dry the weighed gravel, and put the dried gravel, cement, standard sand, water and fluorescent powder together Put it into a mixer for stirring, and after stirring evenly, put the mixture into a mold, remove the mold after 24 hours, and then put the test block into a standard curing box for curi...
Embodiment 3
[0022] (a) CaO:xDy 3+ , yNa + Preparation of phosphor powder: CaCO 3 , Na 2 CO 3 (both are analytically pure) and Dy 2 o 3 (99.99%, analytically pure) according to the molar ratio Ca:Dy:Na=l:0.02:0.2, accurately weighed, added a small amount of ethanol (as a grinding aid), fully ground evenly, and dried in an oven at 110°C for 3 hours. The precursor was obtained, calcined at 1150°C for 3 hours, cooled, and ground to obtain white powder phosphor; (b) Preparation of luminous concrete: according to the mass percentage of each component, phosphor powder 8%, white cement 18%, standard sand 27% %, stone 39%, water 8% and accurately weigh various substances; clean the weighed gravel and dry it, put the dried gravel, cement, standard sand, water and fluorescent powder into the mixer together Stir in the medium, stir the mixture evenly, put the mixture into the mold, remove the mold after 24 hours, and then put the test block into the standard curing box for curing.
[0023] In...
PUM
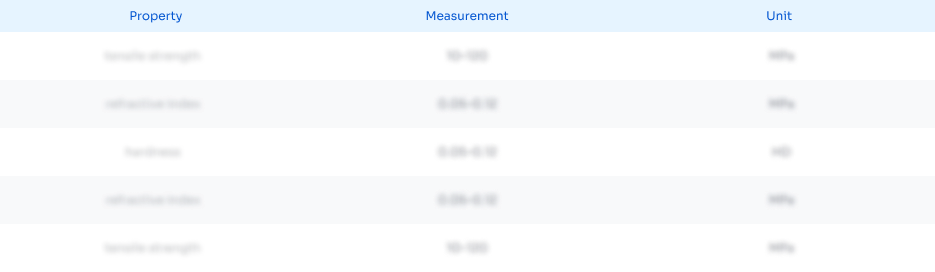
Abstract
Description
Claims
Application Information

- R&D
- Intellectual Property
- Life Sciences
- Materials
- Tech Scout
- Unparalleled Data Quality
- Higher Quality Content
- 60% Fewer Hallucinations
Browse by: Latest US Patents, China's latest patents, Technical Efficacy Thesaurus, Application Domain, Technology Topic, Popular Technical Reports.
© 2025 PatSnap. All rights reserved.Legal|Privacy policy|Modern Slavery Act Transparency Statement|Sitemap|About US| Contact US: help@patsnap.com