Integrated system equipment for desulfurization and denitrification of flue gas
A desulfurization, denitrification and flue gas technology, applied in chemical instruments and methods, dispersed particle separation, dispersed particle filtration, etc. , The effect of less machinery and equipment and less consumption of consumables
- Summary
- Abstract
- Description
- Claims
- Application Information
AI Technical Summary
Problems solved by technology
Method used
Image
Examples
Embodiment Construction
[0025] The present invention will be further described below in conjunction with accompanying drawing and embodiment:
[0026] Such as figure 1 The flue gas desulfurization and denitrification integrated system equipment shown includes absorption tower 1 , bag filter 2 , induced draft fan 3 and chimney 4 connected in sequence. Among them: the absorption tower 1 is a variable-speed dragging absorption tower, and the specific structure is: a Venturi pipe section is arranged in the absorption tower 1, and an expansion section is arranged on the upper part of the Venturi pipe section, and the flue gas enters the Venturi pipe section at the bottom of the absorption tower 1. The inner pipe section accelerates, and the flue gas accelerates to form a fluidized zone.
[0027] The integrated system equipment also includes an absorbent silo 5, an adsorbent silo 6, and a humidification mechanism 7, and the absorbent silo 5 and the adsorbent silo 6 are all connected to the Venturi ...
PUM
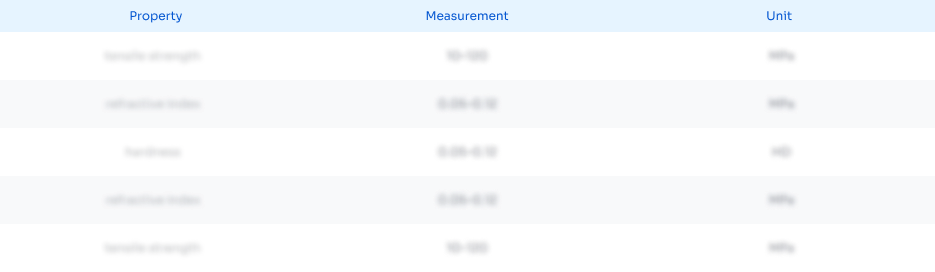
Abstract
Description
Claims
Application Information

- R&D Engineer
- R&D Manager
- IP Professional
- Industry Leading Data Capabilities
- Powerful AI technology
- Patent DNA Extraction
Browse by: Latest US Patents, China's latest patents, Technical Efficacy Thesaurus, Application Domain, Technology Topic, Popular Technical Reports.
© 2024 PatSnap. All rights reserved.Legal|Privacy policy|Modern Slavery Act Transparency Statement|Sitemap|About US| Contact US: help@patsnap.com