Mechanism for changing conduction direction of ultrasonic wave
A technology of transmission direction and ultrasonic wave, applied in the field of mechanisms that change the transmission direction of ultrasonic waves, can solve problems such as complex structure, and achieve the effects of simple device structure, reduced distance, and enhanced hardness
- Summary
- Abstract
- Description
- Claims
- Application Information
AI Technical Summary
Problems solved by technology
Method used
Image
Examples
Embodiment 1
[0020] The present invention comprises a horn 2 and a rocker arm 1, one end of the rocker arm 1 is in contact with the head of the horn 2, the other end opposite to the end is perpendicular to the workpiece to be processed, and the center of the other end The angle between the line and the center line of the horn 2 is greater than 0 degrees. The rocker arm 1 is set on the housing 4 through the rocker shaft 3, the horn 2 is connected with the transducer, the rocker arm 1, the horn 2 and the transducer are all set in the housing 4, and the control box 5 is connected through the wire It is connected with the transducer in the shell 4. The rocker arm 1 can also be arranged outside the casing 4 .
[0021] One or both ends of the rocker arm 1 are ball joint structures. The original output amplitude of the ultrasonic wave can be adjusted by the length of the two ends of the rocker arm 1 using the lever principle.
[0022] A through hole can be set on the rocker arm 1, and the rock...
Embodiment 2
[0025] Such as figure 1 As shown, the present invention includes a horn 2 and a rocker arm 1, one end of the rocker arm 1 is in contact with the head of the horn 2, the other end opposite to the end is perpendicular to the workpiece to be processed, and the other end The centerline of the horn is perpendicular to the centerline of the horn 1. The rocker arm 1 is set on the housing 4 through the pin shaft 3, the horn 2 is connected with the transducer, the rocker arm 1, the horn 2 and the transducer are all arranged in the housing 4, the control box 5 is connected with the The transducers in the casing 4 are connected. The rocker arm 1 can also be arranged outside the casing 4 .
[0026] One or both ends of the rocker arm 1 are ball joint structures. The original output amplitude of the ultrasonic wave can be adjusted by the length of the two ends of the rocker arm 1 using the lever principle.
[0027] A through hole can be set on the rocker arm 1, and the rocker arm 1 can...
PUM
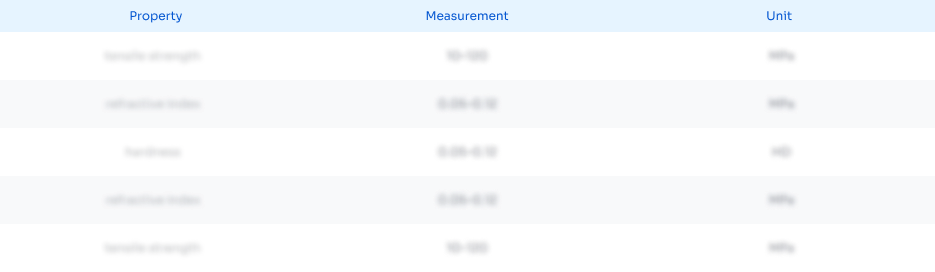
Abstract
Description
Claims
Application Information

- R&D
- Intellectual Property
- Life Sciences
- Materials
- Tech Scout
- Unparalleled Data Quality
- Higher Quality Content
- 60% Fewer Hallucinations
Browse by: Latest US Patents, China's latest patents, Technical Efficacy Thesaurus, Application Domain, Technology Topic, Popular Technical Reports.
© 2025 PatSnap. All rights reserved.Legal|Privacy policy|Modern Slavery Act Transparency Statement|Sitemap|About US| Contact US: help@patsnap.com