Section bending blank manufacturing method of iron-based high temperature alloy flash welding thin wall ring piece
A technology of iron-based superalloy and flash welding, which is applied in the field of profile bending billet making of iron-based superalloy flash welding thin-walled ring parts, can solve the problems of high cost, affecting the dimensional accuracy of ring parts, and large ellipticity of ring parts, etc., to eliminate Ovality, improving dimensional accuracy and processing quality, saving man-hours and energy consumption
- Summary
- Abstract
- Description
- Claims
- Application Information
AI Technical Summary
Problems solved by technology
Method used
Image
Examples
specific Embodiment approach
[0054] The main chemical element content (percentage by weight) of the alloy is: C content ≤ 0.06%, Si content 0.07% ~ 0.35%, Ni content 35.0% ~ 40.0%, Co content 12.0% ~ 16.0%, Nb+ Ta content 4.3%~5.2%, Ti content 1.3%~1.8%, Cr content ≤1.00%, Al content ≤0.20%, Mn content ≤1.00%, Cu content ≤0.50%, B content ≤0.012 %, S content ≤ 0.015%, P content ≤ 0.015%, and the balance is Fe.
[0055] The specific process steps of bending billet are as follows:
[0056] Step 1: Unloading. Such as image 3 As shown, the GH907 alloy material with a rectangular cross section is cut into a profile 20 according to the specifications. The length of the profile 20 is determined according to the diameter of the welding ring, and its maximum cross-sectional area is 65mm (width)×30mm (thickness). This profile 20 is divided into mn, no, op, pq and qw five sections by m, n, o, p, q, w, in order to make the curvature radius of the op section after bending greater than the curvature radius of the n...
PUM
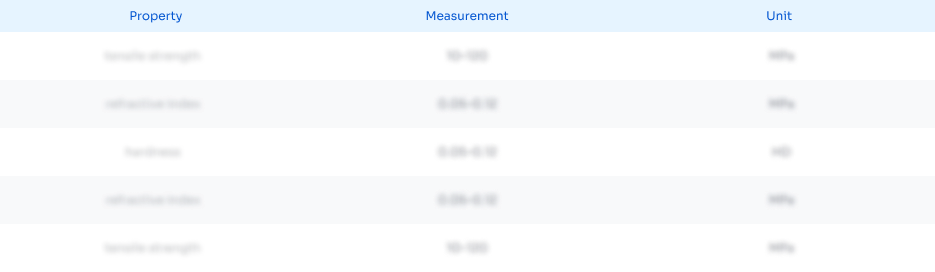
Abstract
Description
Claims
Application Information

- R&D Engineer
- R&D Manager
- IP Professional
- Industry Leading Data Capabilities
- Powerful AI technology
- Patent DNA Extraction
Browse by: Latest US Patents, China's latest patents, Technical Efficacy Thesaurus, Application Domain, Technology Topic, Popular Technical Reports.
© 2024 PatSnap. All rights reserved.Legal|Privacy policy|Modern Slavery Act Transparency Statement|Sitemap|About US| Contact US: help@patsnap.com