Refining method of rice oil
A refining method and rice oil technology, applied in the production/processing of edible oil/fat, etc., can solve the problems of high energy consumption, human health hazards, nutritional value discount, etc., and achieve the effect of high product yield and no waste water discharge.
- Summary
- Abstract
- Description
- Claims
- Application Information
AI Technical Summary
Problems solved by technology
Method used
Image
Examples
Embodiment 1
[0015] The fourth-grade rice bran oil is heated up to 155°C by the heat exchanger, then enters the molecular still, and is evenly distributed on the evaporation surface by the distributor. The temperature of the evaporation surface is 195°C. The light component collection tank, the heavy component directly enters the heavy component collection tank, and the vacuum degree of the decolorization system is at 5Pa. The heavy component enters the first step of fractionation process, heats up to 230°C through a heat exchanger, and then enters a molecular still for refining. The material is evenly distributed on the evaporation surface through a distributor. The temperature of the evaporation surface is 300°C. The temperature is 1Pa, the light component is cooled to 35°C by the built-in condenser, and flows into the semi-finished product collection tank, and the heavy component directly enters the heavy component collection tank, and then enters the second step of fractionation process...
Embodiment 2
[0017] The fourth-grade rice bran oil is heated up to 170°C by the heat exchanger, then enters the molecular still, and is evenly distributed on the evaporation surface by the distributor. The temperature of the evaporation surface is 245°C. The light component collection tank, the heavy component directly enters the heavy component collection tank, and the vacuum degree of the decolorization system is at 40Pa. The heavy component enters the first step of fractionation process, heats up to 250°C through a heat exchanger, and then enters a molecular still for refining. The material is evenly distributed on the evaporation surface by a distributor. The temperature of the evaporation surface is 310°C. The vacuum of the fractionation system The temperature is at 2Pa, the light component is cooled to 42°C through the built-in condenser, and flows into the semi-finished product collection tank, and the heavy component directly enters the heavy component collection tank, and then ente...
Embodiment 3
[0019] The fourth-grade rice bran oil is heated to 165°C through the heat exchanger, then enters the molecular still, and is evenly distributed on the evaporation surface by the distributor. The temperature of the evaporation surface is 195°C. The light component collection tank, the heavy component directly enters the heavy component collection tank, and the vacuum degree of the decolorization system is at 20Pa. The heavy component enters the first step of fractionation process, heats up to 230°C through a heat exchanger, and then enters a molecular still for refining. The material is evenly distributed on the evaporation surface through a distributor. The temperature of the evaporation surface is 300°C. The temperature is 1Pa, the light component is cooled to 35°C by the built-in condenser, and flows into the semi-finished product collection tank, and the heavy component directly enters the heavy component collection tank, and then enters the second step of fractionation proc...
PUM
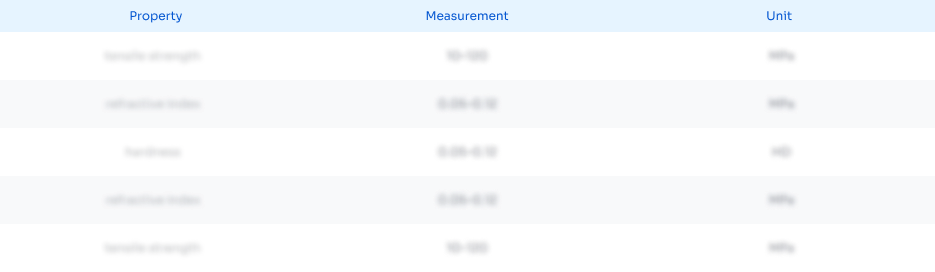
Abstract
Description
Claims
Application Information

- R&D
- Intellectual Property
- Life Sciences
- Materials
- Tech Scout
- Unparalleled Data Quality
- Higher Quality Content
- 60% Fewer Hallucinations
Browse by: Latest US Patents, China's latest patents, Technical Efficacy Thesaurus, Application Domain, Technology Topic, Popular Technical Reports.
© 2025 PatSnap. All rights reserved.Legal|Privacy policy|Modern Slavery Act Transparency Statement|Sitemap|About US| Contact US: help@patsnap.com