Solid bleached sulphate (SBS) coating white cardboard and process for producing the same
A production process and technology for white cardboard, applied in the field of papermaking, can solve the problems of easy failure of anti-counterfeiting measures, high cost, and inability to popularize and implement, and achieve the effects of improving uniformity and surface performance, improving printability and inking performance.
- Summary
- Abstract
- Description
- Claims
- Application Information
AI Technical Summary
Problems solved by technology
Method used
Image
Examples
Embodiment 1
[0034] Surface pulp: wood pulp (weight percentage: bleached hardwood kraft pulp 70%, bleached softwood kraft pulp 30%), crushed and mixed by a pulper, refined by a disc refiner, and entered into the surface of the paper machine net filter;
[0035] Core layer pulp: wood pulp (weight percentage: bleached hardwood kraft pulp 50%, bleached softwood kraft pulp 25%, broken paper 25%), crushed and mixed by a pulper, refined by a disc refiner , enter the paper machine core mesh to filter;
[0036] Bottom pulp: wood pulp (weight percentage: 5% natural fiber, 85% bleached hardwood kraft pulp, 10% bleached softwood kraft pulp), crushed and mixed by a pulper, refined by a disc refiner, Enter the paper machine face mesh for filtration;
[0037] Then, through the three-layer web forming of the paper machine, a wet paper sheet with a surface layer 103, a core layer 102 and a bottom layer 101 distributed with natural fibers is produced. After coating and drying, it enters the coiling sect...
Embodiment 2
[0046] The production process of this embodiment is the same as that of the above-mentioned embodiment 1, the difference lies in: the slurry ratio of the surface layer slurry, the core layer slurry, and the bottom layer slurry, and the coating ratio of the pre-coating and core coating.
[0047] Surface pulp (percentage by weight): bleached hardwood kraft pulp 85%, bleached softwood kraft pulp 15%;
[0048] Core layer pulp (weight percentage): bleached hardwood kraft pulp 53%, bleached softwood kraft pulp 17%, broken paper 30%;
[0049] Bottom pulp (weight percent): natural fiber 8%, bleached hardwood kraft pulp 72%, bleached softwood kraft pulp 20%;
[0050] The coating ratio of precoating and core coating is (parts by weight): 100 parts of calcium carbonate, 8 parts of latex, 3 parts of soybean protein, 0.4 parts of carboxymethyl cellulose, 0.09 parts of dispersant, 0.8 parts of water repellent, lubricating 0.3-1.2 parts of antifoaming agent and 0.035 parts of antifoaming ag...
Embodiment 3
[0056] Surface pulp (percentage by weight): bleached hardwood kraft pulp 90%, bleached softwood kraft pulp 10%;
[0057] Core pulp (weight percent): 55% bleached hardwood kraft pulp, 5% bleached softwood kraft pulp, 40% broken paper;
[0058] Bottom pulp (weight percent): natural fiber 10%, bleached hardwood kraft pulp 60%, bleached softwood kraft pulp 30%;
[0059] The coating ratio of pre-coating and core coating is (parts by weight): 100 parts of calcium carbonate, 10 parts of latex, 1.0 parts of soybean protein, 0.6 parts of carboxymethyl cellulose, 0.12 parts of dispersant, 1.0 parts of water-resistant agent, lubricating 1.2 parts of agent, 0.035 parts of defoamer.
[0060] The coating amounts of the precoat layer 104, the core coat layer 105, and the top coat layer 106 were applied at 10 g / m2, 12 g / m2, and 12 g / m2, respectively.
[0061] The produced SBS coated white cardboard is compared with FBB ordinary white cardboard of the same grammage on the market, and its phy...
PUM
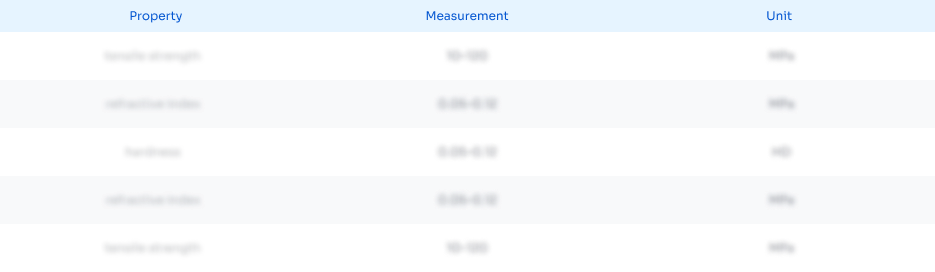
Abstract
Description
Claims
Application Information

- R&D
- Intellectual Property
- Life Sciences
- Materials
- Tech Scout
- Unparalleled Data Quality
- Higher Quality Content
- 60% Fewer Hallucinations
Browse by: Latest US Patents, China's latest patents, Technical Efficacy Thesaurus, Application Domain, Technology Topic, Popular Technical Reports.
© 2025 PatSnap. All rights reserved.Legal|Privacy policy|Modern Slavery Act Transparency Statement|Sitemap|About US| Contact US: help@patsnap.com