Novel Ni-Mn-Ga resin based composite material, and preparation method thereof
A composite material and a new technology, applied in the design scheme and preparation of functional metal particle resin matrix composite materials, in the field of new particle composite materials, can solve the problems of complex process and high equipment requirements, achieve low cost, good mechanics, good material preparation effect of effect
- Summary
- Abstract
- Description
- Claims
- Application Information
AI Technical Summary
Problems solved by technology
Method used
Image
Examples
specific example 1
[0041] Firstly select the elemental components of Ni-Mn-Ga: nickel, manganese, and gallium, and smelt them at low temperature in a vacuum to alloy the elements; slowly raise the temperature to 1450°C for homogenization for 4 minutes, and cool naturally after ingot casting; after cooling, mechanically crush to The small pieces were then vibrated and ball milled for 12 hours, and powders of different sizes were sieved out at intervals to obtain Ni-Mn-Ga powder particles. Then weigh and mix bisphenol A diglycidyl ether epoxy resin (E51) and tetraethylenepentamine at a mass ratio of 100:15, stir for 2 minutes to fully mix the two, and then slowly introduce the powder into the mixed solution Stir the beaker at a speed of 90r / min to disperse the Ni-Mn-Ga powder evenly in the beaker; place the beaker in an ultrasonic cleaner to disperse the particles and remove air bubbles, and slow down the stirring speed to about 60r / min. The process lasts about 10 minutes. Slowly and evenly pour ...
specific example 2
[0043] Firstly select the elemental components of Ni-Mn-Ga: nickel, manganese, gallium, smelt in vacuum at low temperature to alloy the elemental substances; slowly raise the temperature to 1450°C and homogenize for 5 minutes, then cool naturally after casting ingots; after cooling, mechanically crush to The small pieces were then vibrated and ball milled for 24 hours, and powders of different sizes were screened out at intervals to obtain Ni-Mn-Ga powder particles. Then weigh and mix bisphenol A diglycidyl ether epoxy resin (E51) and tetraethylenepentamine at a mass ratio of 100:15, stir for 1 minute to fully mix the two, and then slowly introduce the powder into the mixed solution Stir the beaker at a speed of 120r / min to disperse the Ni-Mn-Ga powder evenly in the beaker; place the beaker in an ultrasonic cleaner to disperse the particles and remove air bubbles, and slow down the stirring speed to about 70r / min. The process lasts for about 20 minutes. Slowly and evenly pour...
specific example 3
[0045] Firstly select the elemental components of Ni-Mn-Ga: nickel, manganese, gallium, melt at low temperature in vacuum to alloy the elemental substances; slowly raise the temperature to 1450°C and homogenize for 7 minutes, then cool naturally after casting ingots; after cooling, mechanically crush to The small pieces were then vibrated and ball milled for 24 hours, and powders of different sizes were screened out at intervals to obtain Ni-Mn-Ga powder particles. Then weigh and mix the selected bisphenol A diglycidyl ether epoxy resin (E51) and tetraethylenepentamine at a mass ratio of 100:15, stir for 1.4 minutes to fully mix the two, and then slowly introduce the powder into the mixing container Stir the beaker of the liquid at a speed of 110r / min to disperse the Ni-Mn-Ga powder evenly in the beaker; place the beaker in an ultrasonic cleaner to disperse the particles and remove air bubbles, slow down the stirring speed to about 65r / min, This process lasts about 15 minutes....
PUM
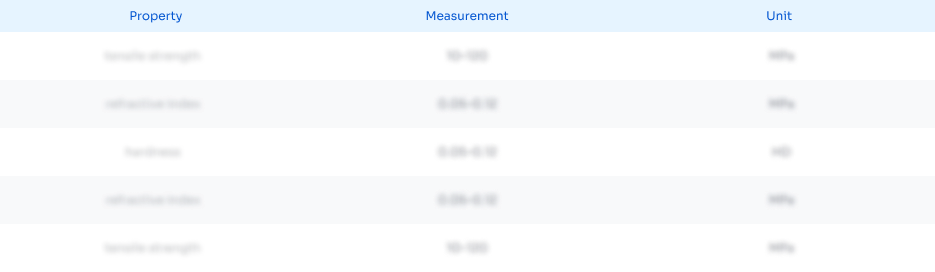
Abstract
Description
Claims
Application Information

- Generate Ideas
- Intellectual Property
- Life Sciences
- Materials
- Tech Scout
- Unparalleled Data Quality
- Higher Quality Content
- 60% Fewer Hallucinations
Browse by: Latest US Patents, China's latest patents, Technical Efficacy Thesaurus, Application Domain, Technology Topic, Popular Technical Reports.
© 2025 PatSnap. All rights reserved.Legal|Privacy policy|Modern Slavery Act Transparency Statement|Sitemap|About US| Contact US: help@patsnap.com