Process for producing trichlorosilane through inverse disporportionation of dichlorosilane
A technology of dichlorodihydrosilicon and trichlorosilane, which is applied to halogenated silicon compounds, halogenated silanes, etc., can solve the problems of loss of silicon element, consumption of large manpower and material resources, uneconomical and other problems, and achieves mild reaction conditions and reduced The effect of small processing costs and system investment
- Summary
- Abstract
- Description
- Claims
- Application Information
AI Technical Summary
Problems solved by technology
Method used
Image
Examples
Embodiment 1
[0028] The gaseous dichlorodihydrogen silicon in the polysilicon production system is condensed through the -20°C frozen brine of the dichloro dihydrogen silicon condenser, and the silicon tetrachloride liquid is cooled by the process water of the silicon tetrachloride cooler. 1:3 into the storage tank for mixing.
[0029] The feed temperature of the mixed raw materials is -10°C, and they are sent into the reactor through a shielded pump for reaction. The reactor is a fixed bed reactor, and it is filled with an anion exchange resin catalyst from Chengdu Nankai Resin Co., Ltd. to control the reaction. The total reaction temperature of the device is 30°C, and the reaction pressure is 0.2MPa. The mixed solution of dichlorodihydrosilane and silicon tetrachloride passes through the catalyst from top to bottom, and the residence time of the liquid raw material in the catalyst packing is 5s, and a part of the reaction raw material occurs Catalyzed reaction deproportionation produces ...
Embodiment 2
[0032] The gaseous dichlorodihydrogen silicon in the polysilicon production system is condensed through the -20°C frozen brine of the dichloro dihydrogen silicon condenser, and the silicon tetrachloride liquid is cooled by the process water of the silicon tetrachloride cooler. 1:3.5 into the storage tank for mixing.
[0033]The feed temperature of the mixed raw materials is 0°C, and they are sent into the reactor through a shielded pump for reaction. The reactor is a fixed-bed reactor, and the anion exchange resin catalyst of Chengdu Nankai Resin Co., Ltd. is filled inside, and the reactor is controlled. The total reaction temperature is 40°C, the reaction pressure is 0.25MPa, the mixture of dichlorodihydrosilane and silicon tetrachloride passes through the catalyst from top to bottom, the residence time of the liquid raw material in the catalyst packing is 6S, and a part of the reaction raw material is catalyzed The reaction deproportionates to generate trichlorosilane. Under...
Embodiment 3
[0035] The gaseous dichlorodihydrogen silicon in the polysilicon production system is condensed through the -20°C frozen brine of the dichloro dihydrogen silicon condenser, and the silicon tetrachloride liquid is cooled by the process water of the silicon tetrachloride cooler. 1:4 into the storage tank for mixing.
[0036] The feed temperature of the mixed raw materials is 10°C, and they are sent into the reactor by shielded pumps for reaction. The reactor is a fixed-bed reactor, and the inside of it is filled with an anion exchange resin catalyst from Dow Chemical Co., Ltd. of the United States. The total reaction temperature of the reactor is 50°C, and the reaction pressure is 0.3MPa. The mixture of dichlorodihydrosilane and silicon tetrachloride passes through the catalyst from top to bottom, and the residence time of the liquid raw material in the catalyst packing is 8S. A part of the reaction raw material Catalytic reaction and disproportionation to generate trichlorosila...
PUM
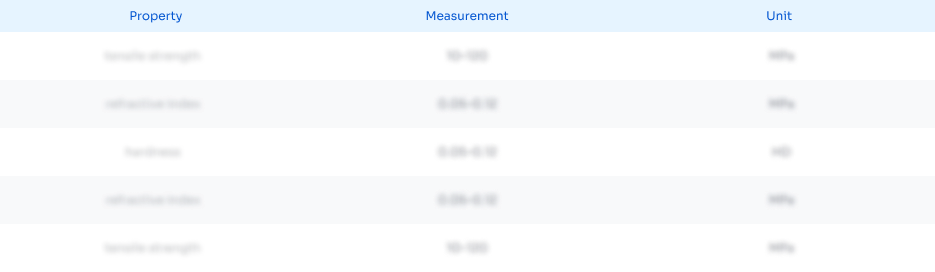
Abstract
Description
Claims
Application Information

- R&D
- Intellectual Property
- Life Sciences
- Materials
- Tech Scout
- Unparalleled Data Quality
- Higher Quality Content
- 60% Fewer Hallucinations
Browse by: Latest US Patents, China's latest patents, Technical Efficacy Thesaurus, Application Domain, Technology Topic, Popular Technical Reports.
© 2025 PatSnap. All rights reserved.Legal|Privacy policy|Modern Slavery Act Transparency Statement|Sitemap|About US| Contact US: help@patsnap.com