Antistatic low-rolling-resistance tyre tread material and preparation method thereof
A low rolling resistance, tire tread technology, applied in the rubber field, can solve the problems of reducing tire rolling resistance, electrostatic accumulation, etc., and achieve the effect of reducing rolling resistance, solving electrostatic accumulation, and improving wet skid resistance and wear resistance.
- Summary
- Abstract
- Description
- Claims
- Application Information
AI Technical Summary
Problems solved by technology
Method used
Image
Examples
Embodiment 1
[0029] Embodiment 1: The formula of antistatic low rolling resistance tire tread material proportion in parts by weight, see Table 2:
[0030] Table 2. Formulation of Example 1
[0031]
[0032] The specific mixing process of composite materials:
[0033] The first stage of mixing: the rotor speed of the internal mixer is 50rpm, and the pressure of the ram is 0.7MPa. First, put the solution-polymerized styrene-butadiene rubber and polybutadiene rubber into the mixing chamber of the internal mixer, and mix for 40 seconds. White carbon black, Put silane coupling agent and silica dispersant into the mixing chamber, continue mixing for 120 seconds, the temperature of the rubber material reaches 120 ° C, lift the weight for 10 seconds, adjust the rotor speed to 30 rpm, and mix with the weight for 90 seconds, the temperature of the rubber material is 150°C, deglue to obtain a section of mixed rubber, and a section of mixed rubber is cooled to room temperature in air.
[0034]Th...
Embodiment 2
[0037] Embodiment 2: The formula of antistatic low rolling resistance tire tread material proportion in parts by weight, see Table 3:
[0038] The formula of table 3 embodiment 2
[0039]
[0040] The specific mixing process of composite materials:
[0041] The first stage of mixing: the rotor speed of the internal mixer is 50rpm, and the pressure of the weight is 0.6MPa. First, put the solution-polymerized styrene-butadiene rubber and polybutadiene rubber into the mixing chamber of the internal mixer, and mix for 35 seconds. White carbon black, Put silane coupling agent and silica dispersant into the mixing chamber, continue mixing for 110 seconds, the temperature of the rubber material reaches 130 °C, lift the weight for 5 seconds, adjust the rotor speed to 30 rpm, and mix with the weight for 90 seconds, the temperature of the rubber material is 145°C, deglue to obtain a section of mixed rubber, and a section of mixed rubber is cooled to room temperature in air.
[0042...
Embodiment 3
[0045] Embodiment 3: The formula of antistatic low rolling resistance tire tread material proportion in parts by weight, see Table 4:
[0046] The formula of table 4 embodiment 3
[0047]
[0048] The specific mixing process of composite materials:
[0049] The first stage of mixing: the rotor speed of the internal mixer is 40rpm, and the pressure of the ballast is 0.7MPa. First, put the solution-polymerized styrene-butadiene rubber and polybutadiene rubber into the mixing chamber of the internal mixer, and mix for 40 seconds. White carbon black, Put silane coupling agent and silica dispersant into the mixing room, continue mixing for 110 seconds, the temperature of the rubber material reaches 120°C, lift the weight for 10 seconds, adjust the rotor speed to 30 rpm, and mix for 100 seconds with the weight, the temperature of the rubber material is 150°C, deglue to obtain a section of mixed rubber, and a section of mixed rubber is cooled to room temperature in air.
[0050]...
PUM
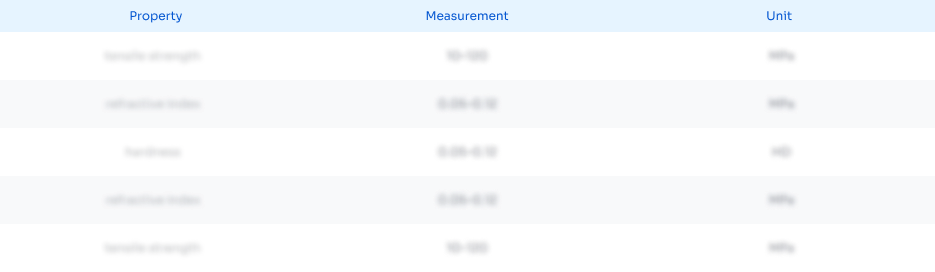
Abstract
Description
Claims
Application Information

- R&D Engineer
- R&D Manager
- IP Professional
- Industry Leading Data Capabilities
- Powerful AI technology
- Patent DNA Extraction
Browse by: Latest US Patents, China's latest patents, Technical Efficacy Thesaurus, Application Domain, Technology Topic, Popular Technical Reports.
© 2024 PatSnap. All rights reserved.Legal|Privacy policy|Modern Slavery Act Transparency Statement|Sitemap|About US| Contact US: help@patsnap.com