Wool drafting and thinning technique
A process and drafting technology, applied in the field of wool stretching technology, can solve the problems of mechanical damage of wool fibers, affecting fiber properties, inconsistent movement of surface and core fibers, etc., to reduce mechanical damage, high production rate, and difficult The effect of slipping or breaking
- Summary
- Abstract
- Description
- Claims
- Application Information
AI Technical Summary
Problems solved by technology
Method used
Examples
Embodiment 1
[0036] A wool fiber refinement process, the process flow is as follows:
[0037] 1. Arranging raw wool into uniform and continuous thin strips or flake-like wool fiber aggregates, immersing in 60°C, 5wt% sodium bisulfite solution for 20 minutes, washing, so that the secondary bonds between the main chains of wool fiber macromolecules, the salt form Spatial transverse linkages such as bonds and hydrogen bonds are opened, so that the wool fiber can be stretched;
[0038] 2. The wool fiber aggregates treated in step 1 pass through a 20wt% polyvinyl alcohol colloid tank, and under the extrusion and traction of a pair of nip rollers, the wool fiber aggregates are evenly coated with polyvinyl alcohol colloids;
[0039] 3. The wool aggregate after being coated with polyvinyl alcohol colloid passes through the Glauber's salt bath tank with a concentration of 420g / l at 40-45°C, and the colloid is solidified under the condition that the wool fiber aggregate has tension;
[0040] 4. In ...
Embodiment 2
[0044] A wool fiber refinement process, the process flow is as follows:
[0045] 1. Arranging raw wool into uniform and continuous thin strips or flake-like wool fiber aggregates, immersing in 60°C, 5wt% sodium bisulfite solution for 20 minutes, washing, so that the secondary bonds between the main chains of wool fiber macromolecules, the salt form Spatial transverse linkages such as bonds and hydrogen bonds are opened, so that the wool fiber can be stretched;
[0046] 2. The wool fiber aggregates treated in step 1 pass through a 14wt% polyvinyl alcohol colloid tank, and under the extrusion and traction of a pair of nip rollers, the wool fiber aggregates are evenly coated with polyvinyl alcohol colloids;
[0047] 3. The wool aggregate after being coated with polyvinyl alcohol colloid passes through the Glauber's salt bath bath with a concentration of 420g / l, and the colloid is solidified under the condition that the wool fiber aggregate has tension;
[0048] 4. In the Glauber...
Embodiment 3
[0053] 1. Arranging raw wool into uniform and continuous thin strips or flake-like wool fiber aggregates, immersing in 60°C, 5wt% sodium bisulfite solution for 20 minutes, washing, so that the secondary bonds between the main chains of wool fiber macromolecules, the salt form Spatial transverse linkages such as bonds and hydrogen bonds are opened, so that the wool fiber can be stretched;
[0054] 2. The wool fiber aggregates treated in step 1 pass through a 17wt% polyvinyl alcohol colloid tank, and under the extrusion and traction of a pair of nip rollers, the wool fiber aggregates are evenly coated with polyvinyl alcohol colloids;
[0055] 3. The wool aggregate after the polyvinyl alcohol colloid is passed through the NaOH bath tank with a concentration of 30wt%, and the colloid is solidified under the condition that the wool fiber aggregate has tension;
[0056] 4. Dry hot drawing: the wool aggregate is heated to 120-140°C through multiple drawing rollers heated by electric ...
PUM
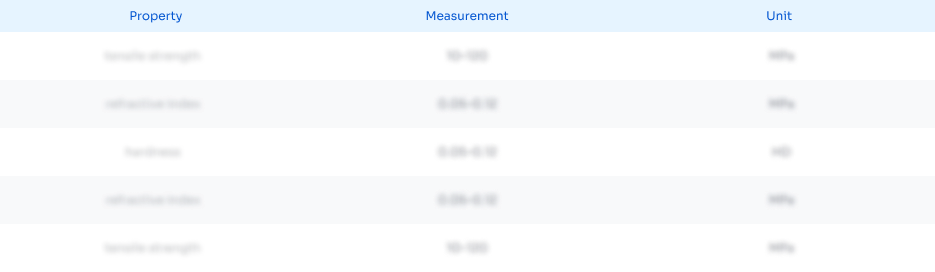
Abstract
Description
Claims
Application Information

- R&D
- Intellectual Property
- Life Sciences
- Materials
- Tech Scout
- Unparalleled Data Quality
- Higher Quality Content
- 60% Fewer Hallucinations
Browse by: Latest US Patents, China's latest patents, Technical Efficacy Thesaurus, Application Domain, Technology Topic, Popular Technical Reports.
© 2025 PatSnap. All rights reserved.Legal|Privacy policy|Modern Slavery Act Transparency Statement|Sitemap|About US| Contact US: help@patsnap.com