Nano attapulgite/nano ferrite composite material and preparation method thereof
A technology of nano-attapulgite and nano-ferrite, which is applied in the field of nano-ferrite composite materials and its preparation, can solve the problems of ferrite crystal grain agglomeration, achieve uniform particle size, abundant raw materials, and excellent ion exchange capacity Effect
- Summary
- Abstract
- Description
- Claims
- Application Information
AI Technical Summary
Problems solved by technology
Method used
Image
Examples
Embodiment 1
[0019] (1) x is 0, and the molecular formula of nanoferrite is BaMnMgFe 16 o 27 . Using the co-precipitation method, first the raw material 0.005mol of BaCl 2 2H 2 O, 0.005mol of MnCl 2 2H 2 O, 0.005mol of MgCl 2 ·6H 2 O and 0.08mol FeCl 3 ·6H 2 O add NaOH-Na 2 CO 3 In the buffer solution, let it stand for precipitation, where n(BaCl 2 2H 2 O): n(MnCl 2 2H 2 O): n(MgCl 2 ·6H 2 O): n(FeCl 3 ·6H 2 (0)=1:1:1:16, then the precipitate is transferred to a beaker, washed with water, filtered and dried to obtain the original nano-ferrite powder;
[0020] (2) Add 0.1 g of water-soluble polymer silane coupling agent dropwise to 100 g of deionized water, adjust the pH value of the system to 4 with a hydrochloric acid solution with a mass percent content of 5%, and obtain a water-soluble polymer silane coupling agent. Then add 1 gram of nano-attapulgite, heat up to 60°C, then add 4 grams of nano-ferrite raw powder prepared in step (1), keep stirring for 1 hour, vacuum f...
Embodiment 2
[0023] (1) x is 0.2, and the molecular formula of nanoferrite is BaMnMgAl 0.2 Fe 15.8 o 27 . Using the co-precipitation method, first the raw material 0.005mol of BaCl 2 2H 2 O, 0.005mol of MnCl 2 2H 2 O, 0.005mol of MgCl 2 ·6H 2 O, 0.079mol of FeCl 3 ·6H 2 O and 0.001mol of AlCl 3 Add NaOH-Na 2 CO 3 In the buffer solution, let it stand for precipitation, where n(BaCl 2 2H 2 O): n(MnCl 2 2H 2 O): n(MgCl 2 ·6H 2 O): n(AlCl 3 ): n(FeCl 3 ·6H 2 (0)=1:1:1:0.2:15.8, then the precipitate is transferred to a beaker, washed with water, filtered and dried to obtain the original powder of nano-ferrite;
[0024] (2) Add 0.2 g of water-soluble polymer silane coupling agent dropwise to 100 g of deionized water, and adjust the pH of the system to 5 with a hydrochloric acid solution with a mass percent content of 10%, to obtain a water-soluble polymer silane coupling agent. Then add 3 grams of nano-attapulgite, then add 7.5 grams of nano-ferrite raw powder prepared in s...
Embodiment 3
[0027] (1) x is 0.4, and the molecular formula of nanoferrite is BaMnMgAl 0.4 Fe 15.6 o 27 . Using the co-precipitation method, first the raw material 0.005mol of BaCl 2 2H 2 O, 0.005mol of MnCl 2 2H 2 O, 0.005mol of MgCl 2 ·6H 2 O, 0.078mol of FeCl 3 ·6H 2O and 0.002mol of AlCl 3 Add NaOH-Na 2 CO 3 In the buffer solution, let it stand for precipitation, where n(BaCl 2 2H 2 O): n(MnCl 2 2H 2 O): n(MgCl 2 ·6H 2 O): n(AlCl 3 ): n(FeCl 3 ·6H 2 (0)=1:1:1:0.4:15.6, then the precipitate is transferred to a beaker, washed with water, filtered and dried to obtain the original nano-ferrite powder;
[0028] (2) Add 0.3 grams of water-soluble polymer silane coupling agent dropwise to 100 grams of deionized water, adjust the pH of the system to 5 with a hydrochloric acid solution with a mass percentage of 15%, and obtain a water-soluble polymer silane coupling agent. Then add 6 grams of nano-attapulgite, heat up to 90°C, then add 6 grams of nano-ferrite raw powder pr...
PUM
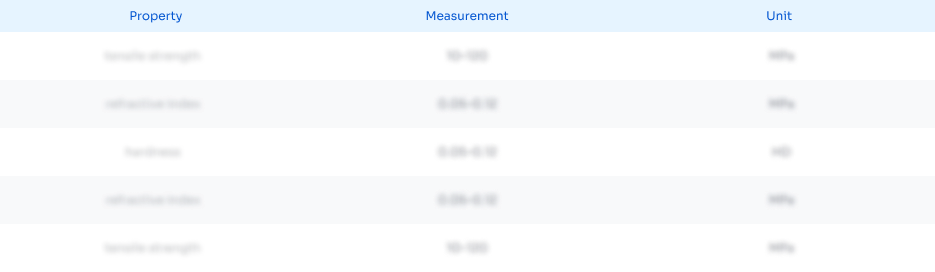
Abstract
Description
Claims
Application Information

- R&D
- Intellectual Property
- Life Sciences
- Materials
- Tech Scout
- Unparalleled Data Quality
- Higher Quality Content
- 60% Fewer Hallucinations
Browse by: Latest US Patents, China's latest patents, Technical Efficacy Thesaurus, Application Domain, Technology Topic, Popular Technical Reports.
© 2025 PatSnap. All rights reserved.Legal|Privacy policy|Modern Slavery Act Transparency Statement|Sitemap|About US| Contact US: help@patsnap.com