Staining method for wet spinning of acrylic fibers
A technology of wet spinning and acrylic fiber, which is applied in the step-by-step coloring field of wet spinning, which can solve the problems of low color fastness, low pigment concentration, and large addition amount, etc., and achieve cumbersome process operation, easy coloring, colorful effect
- Summary
- Abstract
- Description
- Claims
- Application Information
AI Technical Summary
Problems solved by technology
Method used
Examples
Embodiment 1
[0033] According to the weight ratio of the following materials, cationic dye 0.01%, acetic acid (concentration 98%) 0.5%, leveling agent Pingpingjia-O (ie Peregal-O, fatty alcohol polyoxyethylene ether) 0.05%, deionized water 99.44% , prepared into a dye bath with a pH of 6.0 for use; immerse the modified polyacrylonitrile raw material in the above dye bath, and adopt the temperature control method for dyeing, the dyeing starting temperature is set at 50°C, and the temperature is raised at a heating rate of 0.5°C / min to 80°C, heat-dye for 15 minutes, then heat up to 90°C at a rate of 0.1°C / min, heat-dye for 20 minutes, heat up to 100°C and then boil for 45 minutes, and finally slowly drop to 50°C within 20 minutes, and the modified The polyacrylonitrile raw material was taken out, washed with water, and then dried in an oven at 80°C for use.
[0034] Add 0.3w% polyurethane type polymer dispersant, 0.1w% dustproof agent fumed silica and 0.1w% matting agent superfine silica to ...
Embodiment 2
[0037] The following materials are prepared by weight ratio, cationic dye 2%, acetic acid (98%) 1%, leveling agent Pingpingjia-O 0.5%, deionized water 96.5%, and are prepared into a dye bath with a pH of 6.5 for use; Immerse the modified polyacrylonitrile raw material in the above-mentioned dyeing bath, and use the controlled temperature rise method to dye. The dyeing starting temperature is set at 70°C, and the temperature is raised to 85°C at a heating rate of 1°C / min, kept for 30 minutes and dyed at 0.5°C Heat up to 95°C at a rate of 1 / min, keep warm for 30 minutes, heat up to 100°C and then boil for 50 minutes, then slowly drop to 50°C within 25 minutes, take out the raw material of modified polyacrylonitrile obtained by exhaust dyeing, wash with water and place at 95°C Oven dry for later use.
[0038]Add the polyurethane type macromolecular dispersant of 3w%, the dustproof agent modified hydrogenated castor oil of 0.5w% and the matting agent talcum powder of 1w% into the ...
Embodiment 3
[0041] Prepare the following materials by weight ratio, cationic dye 5%, acetic acid (98%) 2%, leveling agent Pingpingjia-O2%, deionized water 92%, and prepare a dye bath with a pH of 7 for use; the modified The polyacrylonitrile raw material is immersed in the above-mentioned dyeing bath, and is dyed by the controlled temperature rise method. The dyeing starting temperature is set at 80°C, and the temperature is raised to 90°C at a heating rate of 2°C / min. Raise the temperature to 95°C, keep warm for 60 minutes, heat up to 100°C and boil for 60 minutes, and finally drop to 50°C slowly within 30 minutes, take out the modified polyacrylonitrile raw material obtained by exhaust dyeing, wash it with water, and dry it in an oven at 110°C stand-by.
[0042] Add 8w% of polyurethane polymer dispersant, 2w% of N-methylpyrrolidone solution of dustproof agent modified polyurea and 2w% of matting agent titanium dioxide into the stirring tank, and add 73w% of solvent dimethyl Sulfoxide (...
PUM
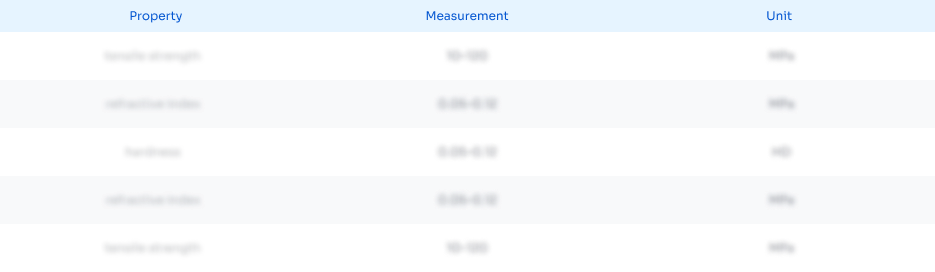
Abstract
Description
Claims
Application Information

- R&D Engineer
- R&D Manager
- IP Professional
- Industry Leading Data Capabilities
- Powerful AI technology
- Patent DNA Extraction
Browse by: Latest US Patents, China's latest patents, Technical Efficacy Thesaurus, Application Domain, Technology Topic, Popular Technical Reports.
© 2024 PatSnap. All rights reserved.Legal|Privacy policy|Modern Slavery Act Transparency Statement|Sitemap|About US| Contact US: help@patsnap.com