Device and method for dry and energy-saving production of polyaluminum chloride water purifying agent
A technology of polyaluminum chloride and water purifier, applied in aluminum chloride, dry gas layout, aluminum halide, etc., can solve the problems of coal combustion utilization rate of only about 85%, thermal efficiency of only 65%, and too high requirements.
- Summary
- Abstract
- Description
- Claims
- Application Information
AI Technical Summary
Problems solved by technology
Method used
Image
Examples
Embodiment 1
[0030] Using aluminum hydroxide, calcium aluminate and hydrochloric acid as raw materials, add 1000Kg of aluminum hydroxide, 4000kg of 31% hydrochloric acid and 2500kg of water into a 10000L enamel reaction kettle, and react under 0.2MPa pressure for 2 hours, then cool down to 100°C, add 1000kg of calcium aluminate was reacted for another 1.5 hours, and then filtered to obtain liquid polyaluminum chloride with an alumina content of 13.5%. The liquid polyaluminum chloride with an alumina content of 13.5% is used as raw material for spray drying. The flue gas temperature at the outlet of the fluidized fluidized furnace is 750°C-800°C. After the second heat exchange, the flue gas temperature decreases by 100°C-120°C. After the second heat exchange, it is heated to 250°C-260°C as dry hot air. After the hot air passes through the drying tower to dry the material, the temperature of leaving the drying tower is 110°C-118°C. The tail gas at this temperature is used as the pre-drying co...
Embodiment 2
[0032] Using aluminum hydroxide and hydrochloric acid as raw materials, add 3600Kg of aluminum hydroxide, 7600kg of 31% hydrochloric acid and 500kg of water in a 10000L enamel reaction kettle, and react at a pressure of 0.4MPa for 4 hours, then cool down to 100°C, and filter to obtain the content of alumina It is 18.0% liquid polyaluminum chloride. The liquid polyaluminum chloride with an alumina content of 18.0% is used as raw material for spray drying. The flue gas temperature at the outlet of the fluidized fluidized furnace is 750°C-800°C. After the second heat exchange, the flue gas temperature decreases by 100°C-120°C. After the second heat exchange, it is heated to 230°C-240°C as dry hot air. After the hot air passes through the drying tower to dry the material, the temperature of leaving the drying tower is 105°C-110°C. The tail gas at this temperature is used as the pre-drying concentration tower. Hot air can increase the liquid polyaluminum chloride with alumina conte...
Embodiment 3
[0034] Using bauxite, calcium aluminate and hydrochloric acid as raw materials, add bauxite 2300kg, 31% hydrochloric acid 4000kg and water 2500kg in a 10000L reaction tank, react at 100°C for 3 hours, add calcium aluminate 1000kg, and then react for 1.5 hour, then filtered to obtain aluminum oxide content of 13.5% of the liquid polyaluminum chloride. The liquid polyaluminum chloride with an alumina content of 13.5% is used as raw material for spray drying. The flue gas temperature at the outlet of the fluidized fluidized furnace is 750°C-800°C. After the second heat exchange, the flue gas temperature decreases by 100°C-120°C. After the second heat exchange, it is heated to 250°C-260°C as dry hot air. After the hot air passes through the drying tower to dry the material, the temperature of leaving the drying tower is 110°C-118°C. The tail gas at this temperature is used as the pre-drying concentration tower. Hot air can increase the liquid polyaluminum chloride with alumina con...
PUM
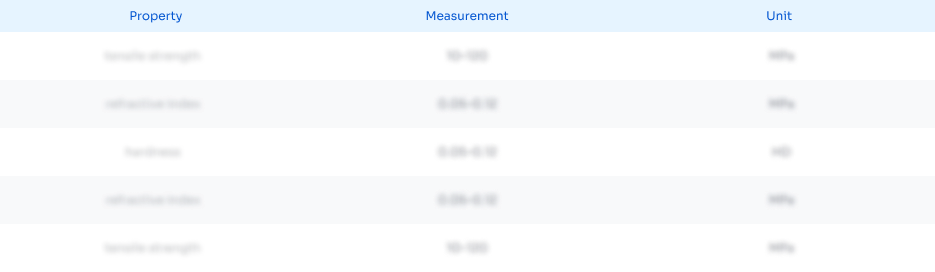
Abstract
Description
Claims
Application Information

- R&D Engineer
- R&D Manager
- IP Professional
- Industry Leading Data Capabilities
- Powerful AI technology
- Patent DNA Extraction
Browse by: Latest US Patents, China's latest patents, Technical Efficacy Thesaurus, Application Domain, Technology Topic, Popular Technical Reports.
© 2024 PatSnap. All rights reserved.Legal|Privacy policy|Modern Slavery Act Transparency Statement|Sitemap|About US| Contact US: help@patsnap.com