Gasoline desulfurization method
A gasoline and hydrodesulfurization technology, which is applied in the petroleum industry, hydrocarbon oil treatment, and hydrotreating process, etc., can solve problems such as difficult to obtain products, difficult air, and inconspicuous desulfurization effect, and achieve the effect of improving the effect
- Summary
- Abstract
- Description
- Claims
- Application Information
AI Technical Summary
Problems solved by technology
Method used
Image
Examples
Embodiment 1
[0101] This example is used to illustrate the gasoline desulfurization method provided by the present invention.
[0102] In this example, using the attached figure 1 The flow shown in Table 1 treats the raw material FCC gasoline A.
[0103] (1) The cutting fractionation temperature of gasoline A is 75° C. to obtain heavy fractions with relatively high boiling ranges and light fractions with relatively low boiling ranges. After cutting, the yields of light fractions B and heavy fractions C are respectively 40% by weight and 60% by weight. %.
[0104] (2) In the selective hydrogenation system, the heavy fraction is subjected to selective hydrogenation treatment. The conditions for the first selective hydrogenation reaction include: the reaction hydrogen partial pressure is 1.6MPa, the reaction temperature is 240°C, and the liquid hourly space velocity is 3.0h -1 , hydrogen oil volume ratio 300Nm 3 / m 3 . The conditions of the second selective hydrogenation reaction include...
Embodiment 2
[0122] This example is used to illustrate the gasoline desulfurization method provided by the present invention.
[0123] In this example, using the attached figure 1 The flow shown in Table 3 treats the raw material FCC gasoline F.
[0124] (1) The cutting fractionation temperature of gasoline F is 60° C. to obtain a heavy fraction with a relatively high boiling range and a light fraction with a relatively low boiling range. After cutting, the yields of the light fraction G and the heavy fraction H are respectively 36% by weight and 64% by weight. %.
[0125] (2) In the selective hydrogenation system, the reaction temperature of the first selective hydrogenation reaction is 290°C, the reaction temperature of the second selective hydrogenation reaction is 310°C, and the reaction hydrogen to oil volume ratio is 350Nm 3 / m 3 , other conditions are all identical with the step (2) of embodiment 1. The heavy fraction after hydrogenation is divided into two parts, and the weight...
PUM
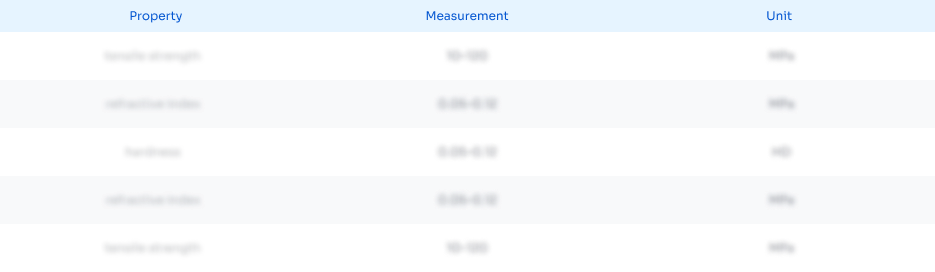
Abstract
Description
Claims
Application Information

- Generate Ideas
- Intellectual Property
- Life Sciences
- Materials
- Tech Scout
- Unparalleled Data Quality
- Higher Quality Content
- 60% Fewer Hallucinations
Browse by: Latest US Patents, China's latest patents, Technical Efficacy Thesaurus, Application Domain, Technology Topic, Popular Technical Reports.
© 2025 PatSnap. All rights reserved.Legal|Privacy policy|Modern Slavery Act Transparency Statement|Sitemap|About US| Contact US: help@patsnap.com