Heat conducting polyamide composite material and preparation method thereof
A composite material and polyamide technology, which is applied in the field of thermally conductive polyamide composite materials and its preparation, can solve the problems of high price, low thermal conductivity and mechanical properties of PA46, and achieve low cost, good processability and low density.
- Summary
- Abstract
- Description
- Claims
- Application Information
AI Technical Summary
Problems solved by technology
Method used
Image
Examples
Embodiment 1
[0035] A PA heat-conducting material, by weight fraction, consists of the following components:
[0036]
[0037] (1) Dry 40 parts of PA6 at 100°C for 4 hours, and dry 58.2 parts of thermally conductive silicon carbide at 100°C for 4 hours;
[0038] (2) Put 58.2 parts of dried thermally conductive silicon carbide into the high-speed mixer, and spray a mixture of 0.5 parts of coupling agent and 0.5 part of white oil into 58.2 parts of thermally conductive silicon carbide in the high-speed mixer Mix at high speed for 30 minutes, dry at 100°C for 3 hours before use;
[0039] (3) Put 40 parts of dried PA6, 0.1 part of antioxidant 1098, 0.2 part of antioxidant 168, 0.2 part of EBS, 0.3 part of processing aid TR065 and the mixture obtained in step 2 into a high-speed mixer, Mix for 15 minutes at room temperature;
[0040] (4) Add the mixture obtained in step (3) into the twin-screw extruder, and the temperatures of the screw 1~6 zones are 180~200°C, 210~230°C, 220~240°C, 230~24...
Embodiment 2
[0046] A PA heat-conducting material, by weight fraction, consists of the following components:
[0047]
[0048] (1) Dry 20 parts of PA resin at 100°C for 4 hours, and dry 77.4 parts of thermally conductive alumina at 100°C for 4 hours;
[0049] (2) Put the dried 77.4 parts of thermally conductive alumina into the high-speed mixer, and add the mixture of 0.7 parts of coupling agent and 0.7 part of white oil to 77.4 parts of thermally conductive alumina in the high-speed mixer by spraying Medium, after mixing at high speed for 30 minutes, dry at 100°C for 3 hours before use;
[0050] (3) Put 20 parts of dried PA6, 0.1 part of antioxidant 1098, 0.1 part of PEPQ, 0.2 part of EBS, 0.6 part of processing aid TR065 and the mixture obtained in step 2 into a high-speed mixer, and at room temperature Mix for 15 minutes;
[0051] (4) Add the mixture obtained in step (3) into the twin-screw extruder, and the temperatures of the screw 1~6 zones are 180~200°C, 210~230°C, 220~240°C, 2...
Embodiment 3
[0056] A PA heat-conducting material, by weight fraction, consists of the following components:
[0057]
[0058] (1) Dry 27.6 parts of PA6 resin at 100°C for 4 hours, dry 40 parts of thermally conductive alumina and 35 parts of thermally conductive silicon carbide at 100°C for 4 hours;
[0059] (2) Put 40 parts of dried alumina and 35 parts of thermally conductive silicon carbide into the high-speed mixer, and add the mixture of 0.7 parts of coupling agent and 0.7 parts of white oil into the high-speed mixer by spraying 40 parts of thermally conductive alumina and 35 parts of thermally conductive silicon carbide were mixed at high speed for 30 minutes, dried at 100°C for 3 hours before use;
[0060] (3) Add 27.6 parts of dried PA6, 0.1 part of antioxidant 1098, 0.1 part of PEPQ, 0.6 part of processing aid TR065 and the mixture obtained in step 2 into a high-speed mixer, and mix at room temperature for 15 minutes;
[0061] (4) Add the mixture obtained in step (3) into the ...
PUM
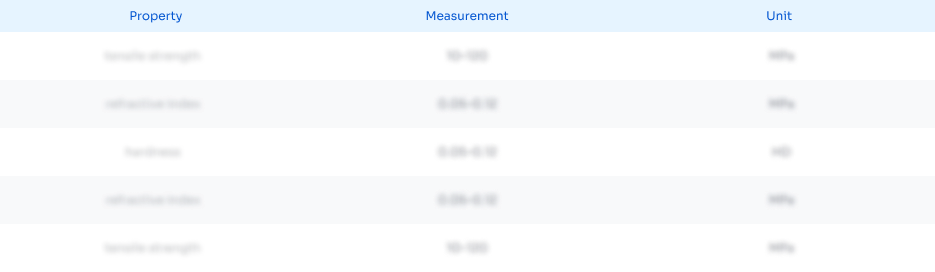
Abstract
Description
Claims
Application Information

- R&D
- Intellectual Property
- Life Sciences
- Materials
- Tech Scout
- Unparalleled Data Quality
- Higher Quality Content
- 60% Fewer Hallucinations
Browse by: Latest US Patents, China's latest patents, Technical Efficacy Thesaurus, Application Domain, Technology Topic, Popular Technical Reports.
© 2025 PatSnap. All rights reserved.Legal|Privacy policy|Modern Slavery Act Transparency Statement|Sitemap|About US| Contact US: help@patsnap.com