Waste-carbon-fiber-reinforced polybutylene terephthalate composite material and preparation method thereof
A technology of polybutylene terephthalate and composite materials, which is applied in the field of improving the interface performance between fibers and substrates, can solve the problems of expensive carbon fibers, etc., and achieve good market prospects, high toughness, and good conductivity Effect
- Summary
- Abstract
- Description
- Claims
- Application Information
AI Technical Summary
Problems solved by technology
Method used
Image
Examples
example 1
[0027] First put the carbon fiber waste silk in a nitric acid solution with a mass percentage concentration of 37% for 2 hours, then wash it with clean water, and then put the carbon fiber waste silk in an epoxy resin solution with a mass percentage concentration of 3 wt.% for 5 hours. Hours, the solvent is a solution of water and ethanol with a volume ratio of 1:1. After the epoxy resin is fully adsorbed on the carbon fiber, it is then fully dried in a vacuum oven at 90°C. Weigh polybutylene terephthalate, carbon fiber waste, toughening agent, and antioxidant according to the following mass percentages.
[0028]
[0029] The polybutylene terephthalate, the toughening agent and the antioxidant are placed in the mixer and mixed evenly, and then the mixed materials are fed into the twin-screw extruder through a hopper. At the same time, the carbon fiber waste after surface treatment is fed from the exhaust port located in the middle of the barrel through a side feeding device...
example 2
[0031] First put the carbon fiber waste silk in a nitric acid solution with a mass percentage concentration of 37% for 2 hours, then wash it with clean water, and then put the carbon fiber waste silk in an epoxy resin solution with a mass percentage concentration of 3 wt.% for 5 hours. Hours, the solvent is a solution of water and ethanol with a volume ratio of 1:1. After the epoxy resin is fully adsorbed on the carbon fiber, it is then fully dried in a vacuum oven at 90°C. Weigh polybutylene terephthalate, carbon fiber waste, toughening agent, and antioxidant according to the following mass percentages.
[0032]
[0033] Put the weighed polybutylene terephthalate, toughening agent and antioxidant in the mixer and mix evenly, then feed the mixed materials into the twin-screw extruder through the hopper. At the same time, the carbon fiber waste after surface treatment is fed from the exhaust port located in the middle of the barrel through a side feeding device equipped with...
example 3
[0035] First put the carbon fiber waste silk in a nitric acid solution with a mass percentage concentration of 37% for 2 hours, then wash it with clean water, and then put the carbon fiber waste silk in an epoxy resin solution with a mass percentage concentration of 3 wt.% for 5 hours. Hours, the solvent is a solution of water and ethanol with a volume ratio of 1:1. After the epoxy resin is fully adsorbed on the carbon fiber, it is then fully dried in a vacuum oven at 90°C. Weigh polybutylene terephthalate, carbon fiber waste, toughening agent, and antioxidant according to the following mass percentages.
[0036]
[0037] The polybutylene terephthalate, the toughening agent and the antioxidant are placed in the mixer and mixed evenly, and then the mixed materials are fed into the twin-screw extruder through a hopper. At the same time, the carbon fiber waste after surface treatment is fed from the exhaust port located in the middle of the barrel through a side feeding device...
PUM
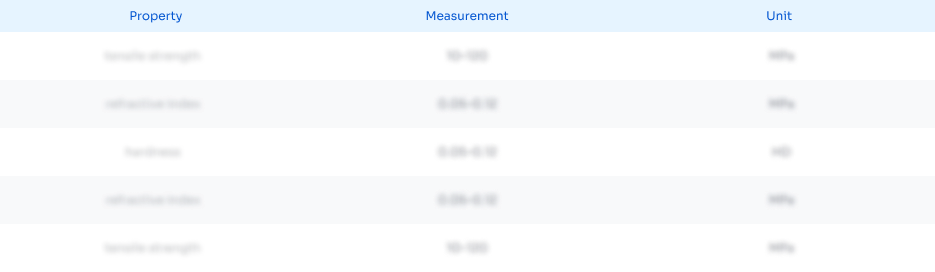
Abstract
Description
Claims
Application Information

- Generate Ideas
- Intellectual Property
- Life Sciences
- Materials
- Tech Scout
- Unparalleled Data Quality
- Higher Quality Content
- 60% Fewer Hallucinations
Browse by: Latest US Patents, China's latest patents, Technical Efficacy Thesaurus, Application Domain, Technology Topic, Popular Technical Reports.
© 2025 PatSnap. All rights reserved.Legal|Privacy policy|Modern Slavery Act Transparency Statement|Sitemap|About US| Contact US: help@patsnap.com