Method and apparatus for simultaneous determination of post-buckling deformation parameters and elastic moduli of elastomeric material
A measuring device and a technique for elastic modulus, applied in the direction of using a stable bending force to test the strength of materials, etc., can solve the problems of low measurement accuracy, inconvenient operation, complex structure, etc., to simplify the calculation process, improve the measurement accuracy, and test operation. simple effect
- Summary
- Abstract
- Description
- Claims
- Application Information
AI Technical Summary
Problems solved by technology
Method used
Image
Examples
Embodiment 1
[0039] Randomly select a certain number of cut into the prescribed length of the sample. start up figure 1 and figure 2 The device, and initialize and proofread the device, input the basic parameters such as the sample name, thickness, width and length through the touch screen 11, as well as the axial displacement determined according to the length of the sample and the F( a , π / 2) (as shown in Table 1) and other setting parameters; locate the dynamic support baffle 6 according to the length of the sample; take a sample 4 and put it between the static support baffle 2 and the dynamic support baffle 6 of the device between figure 1 As shown, start the test system, the linear stepper motor 7 starts to work, and the screw of the linear stepper motor 7 pushes the dynamic support baffle 6 at a speed of 0.01-1.0 mm / s to cause post-buckling deformation of the sample. When the dynamic support baffle 6. The linear stepper motor 7 automatically stops when the specified value of th...
Embodiment 2
[0059] 65Mn steel compression bar post-buckling mid-point deflection, end rotation angle and elastic modulus measurement method: Randomly select 3 samples with a length of 180mm. Start the device, initialize and calibrate the instrument, input the basic parameters such as the sample name is 65Mn steel sheet, the thickness is 0.3mm, the width is 12.5mm and the length is 180mm through the touch screen 10, and the elastic modulus determined according to the sample length 180mm The axial displacement corresponding to the measurement is 12.14mm and F( a , π / 2) (as shown in Table 1) set parameters such as 1.5981; position the dynamic support baffle 6 according to the length of the sample.
[0060] Take a sample 4 and put it between the static support baffle plate 2 and the dynamic support baffle plate 6 of the device. figure 1 As shown, start the test system, the linear motor 7 starts to work, push the dynamic support baffle 6 at a speed of 0.1 mm / s through the linear stepping mot...
Embodiment 3
[0071] Determination of mid-point deflection, end rotation angle and elastic modulus of noodle compression bar post-buckling: randomly select 3 samples with a length of 150 mm. Start the device, initialize and calibrate the instrument, input the basic parameters such as the name of the sample as dried noodles, the thickness of 0.840mm, the width of 3.813mm and the length of 150mm through the touch screen 11, and determine the elastic modulus according to the sample length of 150mm The corresponding axial displacement is 7.09mm and F( a , π / 2) (as shown in Table 1) set parameters such as 1.5898; position the dynamic support baffle 6 according to the length of the sample.
[0072] Take a sample 4 and put it between the static support baffle plate 2 and the dynamic support baffle plate 6 of the device. figure 1 As shown, start the test system, the linear motor 7 starts to work, push the dynamic support baffle 6 at a speed of 0.1 mm / s through the linear stepping motor screw to c...
PUM
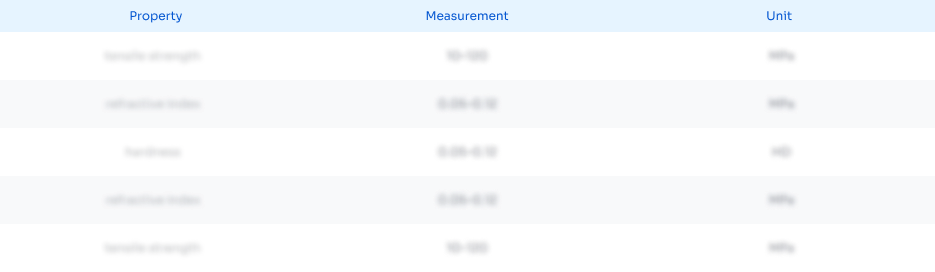
Abstract
Description
Claims
Application Information

- R&D
- Intellectual Property
- Life Sciences
- Materials
- Tech Scout
- Unparalleled Data Quality
- Higher Quality Content
- 60% Fewer Hallucinations
Browse by: Latest US Patents, China's latest patents, Technical Efficacy Thesaurus, Application Domain, Technology Topic, Popular Technical Reports.
© 2025 PatSnap. All rights reserved.Legal|Privacy policy|Modern Slavery Act Transparency Statement|Sitemap|About US| Contact US: help@patsnap.com