Sheath material for optical fiber cable, and production process thereof
A technology of sheath material and optical cable, applied in the direction of fiber mechanical structure, etc., can solve the problem of single performance of optical cable sheath material, achieve low water vapor permeability, improve performance, and meet the requirements of use
- Summary
- Abstract
- Description
- Claims
- Application Information
AI Technical Summary
Problems solved by technology
Method used
Image
Examples
Embodiment 1
[0055] 1) High-density polyethylene, linear low-density polyethylene or low-density polyethylene are mixed and formulated into polyethylene base material, and 86 parts of the polyethylene base material are taken;
[0056] 2) Take 2.4 parts of carbon black to make a master batch, and evenly disperse it in the polyethylene base material;
[0057] 3) Take 0.8 parts of fluorine-containing rheological agent PPA powder and PE base material to make masterbatch, and then add it to polyolefin base material;
[0058] 4) Take 2.4 parts of carbon black masterbatch, 0.6 part of antioxidant, 0.9 part of lubricant, 0.5 part of plastic brightener and 0.8 part of softener and mix evenly, and the mixing time is 8-10 minutes;
[0059] 5) Add the small dose of mixed material in step 4 to 8 parts of modifier EVA and mix for 8-10 minutes;
[0060] 6) Add the mixture in step 5 to the polyethylene base material and mix for 10 minutes;
[0061] 7) Raise the temperature of the extruder to 210°C, add ...
Embodiment 2
[0064] 1) Mix high-density polyethylene, linear low-density polyethylene or low-density polyethylene to prepare a polyethylene base material, and get 85 parts of the polyethylene base material;
[0065] 2) Take 2.5 parts of carbon black to make a master batch, and evenly disperse it in the polyethylene base material;
[0066] 3) Take 1 part of fluorine-containing rheological agent PPA powder and PE base material to make a masterbatch, and then add it to the polyolefin base material;
[0067] 4) Take 2.5 parts of carbon black masterbatch, 0.5 part of antioxidant, 0.5 part of lubricant, 0.5 part of plastic brightener and 1 part of softener and mix evenly, and the mixing time is 8-10 minutes;
[0068] 5) Add the small dose of mixed material in step 4 to 9 parts of modifier EVA and mix for 8-10 minutes;
[0069] 6) Add the mixture in step 5 to the polyethylene base material and mix for 10 minutes;
[0070] 7) Raise the temperature of the extruder to 210°C, add the mixed material...
Embodiment 3
[0073] 1) Mix high-density polyethylene, linear low-density polyethylene or low-density polyethylene to prepare a polyethylene base material, and take 88 parts of the polyethylene base material;
[0074] 2) Take 2.6 parts of carbon black to make a masterbatch, and evenly disperse it in the polyethylene base material;
[0075] 3) Take 0.9 parts of fluorine-containing rheological agent PPA powder and PE base material to make masterbatch, and then add it to polyolefin base material;
[0076] 4) Take 2.6 parts of carbon black masterbatch, 1 part of antioxidant, 0.8 part of lubricant, 0.8 part of plastic brightener and 0.9 part of softener and mix evenly, and the mixing time is 8-10 minutes;
[0077] 5) Add the small dose of mixed material in step 4 to 5 parts of modifier EVA and mix for 8-10 minutes;
[0078] 6) Add the mixture in step 5 to the polyethylene base material and mix for 10 minutes;
[0079] 7) Raise the temperature of the extruder to 210°C, add the mixed material in...
PUM
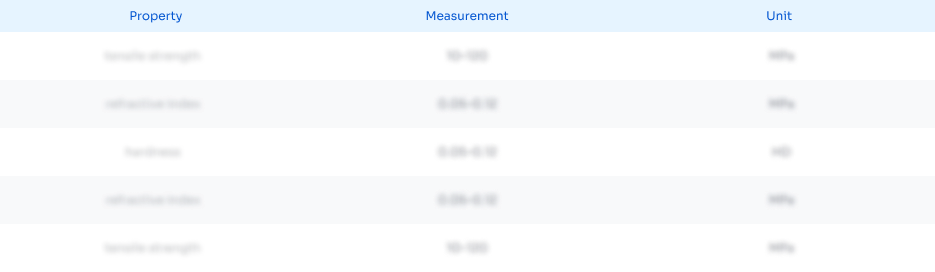
Abstract
Description
Claims
Application Information

- R&D
- Intellectual Property
- Life Sciences
- Materials
- Tech Scout
- Unparalleled Data Quality
- Higher Quality Content
- 60% Fewer Hallucinations
Browse by: Latest US Patents, China's latest patents, Technical Efficacy Thesaurus, Application Domain, Technology Topic, Popular Technical Reports.
© 2025 PatSnap. All rights reserved.Legal|Privacy policy|Modern Slavery Act Transparency Statement|Sitemap|About US| Contact US: help@patsnap.com