High-light-color-fastness transfer printing method
A technology of transfer printing and color fastness, applied in transfer printing method, dyeing method, printing and other directions, can solve the problems of affecting the wearing effect, lightening of pattern color, poor color fastness, etc., to achieve good light resistance, combined with The effect of improving the firmness and preventing the peeling of the printing
- Summary
- Abstract
- Description
- Claims
- Application Information
AI Technical Summary
Problems solved by technology
Method used
Examples
Embodiment 1
[0014] First prepare the ink for transfer printing: mix 40% black disperse dye, 30% red disperse dye, 15% methanol, 10% polyvinyl butyral, 5% light stabilizer 622, and stir Evenly, it is made into ink, and printed on the transfer paper according to a certain flower shape.
[0015] Polyethylene oxide was then mixed with water at a ratio of 1:1000. Overlap the patterned side of the transfer paper with the textile, spray the prepared polyoxyethylene aqueous solution onto the surface of the textile with a high-pressure nozzle, and apply 220°C high-temperature hot pressing for about 30 seconds, then the disperse dye sublimates into a gaseous state. Transfer from paper to fabric.
Embodiment 2
[0017] First prepare the ink for transfer printing: mix 55% black disperse dye, 20% red disperse dye, 13% isobutanol, 8% polyvinyl butyral, 4% light stabilizer 622, And stir it evenly to make ink, and print it on the transfer paper according to a certain flower shape.
[0018] Then mix polyethylene oxide and water at a ratio of 1:5000, overlap the patterned side of the transfer paper with the textile, and spray the prepared polyethylene oxide aqueous solution onto the surface of the textile with a high-pressure nozzle, while applying 220 ℃ high temperature hot pressing for about 40s, the disperse dye sublimates into a gaseous state and transfers from the paper to the fabric.
Embodiment 3
[0020] First prepare the ink for transfer printing: mix 79% black disperse dye, 10% red disperse dye, 12% mixture of methanol and isobutanol (the volume ratio of the two is 1:1), 5% polyvinyl alcohol Butyral and 3% light stabilizer 622 are mixed and stirred evenly to make ink, which is printed on transfer paper in a certain pattern.
[0021] Then mix polyethylene oxide and water at a ratio of 1:10000, overlap the patterned side of the transfer paper with the textile, and spray the prepared polyethylene oxide aqueous solution onto the surface of the textile with a high-pressure nozzle, while applying 220 ℃ high temperature hot pressing for about 60s, the disperse dye sublimates into a gaseous state and transfers from the paper to the fabric.
PUM
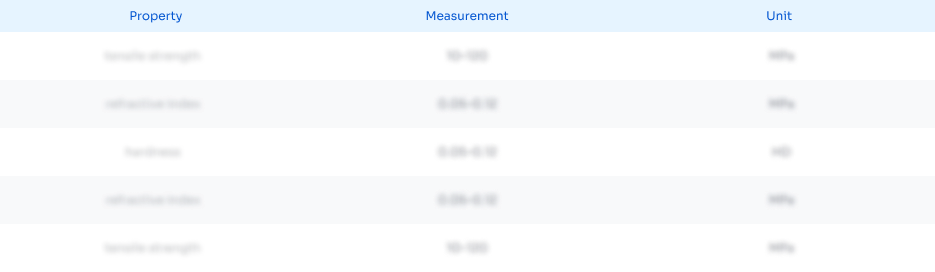
Abstract
Description
Claims
Application Information

- R&D
- Intellectual Property
- Life Sciences
- Materials
- Tech Scout
- Unparalleled Data Quality
- Higher Quality Content
- 60% Fewer Hallucinations
Browse by: Latest US Patents, China's latest patents, Technical Efficacy Thesaurus, Application Domain, Technology Topic, Popular Technical Reports.
© 2025 PatSnap. All rights reserved.Legal|Privacy policy|Modern Slavery Act Transparency Statement|Sitemap|About US| Contact US: help@patsnap.com