Super-nylon 66 alloy prepared by in-situ reactive compatibilization method and preparation method thereof
A nylon and super-tough technology, applied in the field of nylon 66 alloy, can solve the problems of poor mechanical properties of the blend, and achieve the effects of easy popularization and application, easy control, and improved production efficiency
- Summary
- Abstract
- Description
- Claims
- Application Information
AI Technical Summary
Problems solved by technology
Method used
Image
Examples
Embodiment 1
[0050] Super-tough nylon 66 alloy prepared by in-situ reaction compatibilization method is composed of the following raw materials in parts by weight: 90 parts of polyamide 66 (PA66), 10 parts of ethylene and octene copolymer (POE), 2,5-dimethyl - 0.1 part of 2,5-di-tert-butylperoxyhexane (L-101), 0.5 part of maleic anhydride (MAH).
[0051] The method for preparing super-tough nylon 66 alloy by in-situ reaction compatibilization method comprises the following steps:
[0052] (1), the initiator 2,5-dimethyl-2,5-di-tert-butylperoxyhexane and maleic anhydride are dissolved in acetone, and placed for later use;
[0053] (2) Put nylon 66 in a vacuum oven for drying treatment, control the oven temperature at 90°C, dry for 4 hours, place POE in a vacuum oven for drying treatment, control the oven temperature at 70°C, and dry for 4 hours, Nylon 66 and POE were then cooled to room temperature;
[0054] (3), pour the mixed solution of initiator 2,5-dimethyl-2,5-di-tert-butylperoxyhex...
Embodiment 2
[0057] Super-tough nylon 66 alloy prepared by in-situ reaction compatibilization method is composed of the following raw materials in parts by weight: 80 parts of polyamide 66 (PA66), 20 parts of ethylene and octene copolymer (POE), 2,5-dimethyl - 0.5 parts of 2,5-di-tert-butylperoxyhexane (L-101), 2.5 parts of maleic anhydride (MAH).
[0058] The method for preparing super-tough nylon 66 alloy by in-situ reaction compatibilization method, its steps are the same as in Example 1.
Embodiment 3
[0060] Super-tough nylon 66 alloy prepared by in-situ reaction compatibilization method is composed of the following raw materials in parts by weight: 70 parts of polyamide 66 (PA66), 30 parts of ethylene and octene copolymer (POE), 2,5-dimethyl - 0.1 part of 2,5-di-tert-butylperoxyhexane (L-101), 1 part of maleic anhydride (MAH).
[0061] The method for preparing super-tough nylon 66 alloy by in-situ reaction compatibilization method, its steps are the same as in Example 1.
PUM
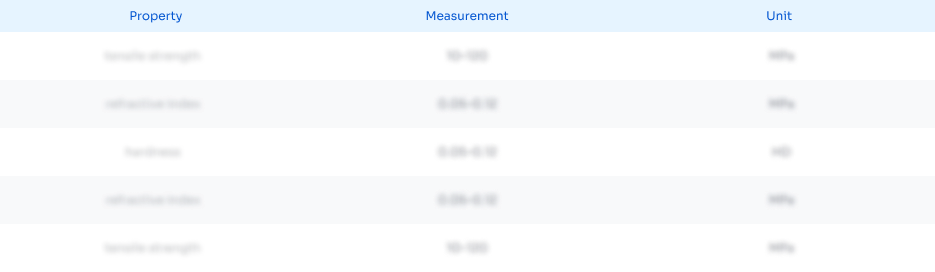
Abstract
Description
Claims
Application Information

- R&D
- Intellectual Property
- Life Sciences
- Materials
- Tech Scout
- Unparalleled Data Quality
- Higher Quality Content
- 60% Fewer Hallucinations
Browse by: Latest US Patents, China's latest patents, Technical Efficacy Thesaurus, Application Domain, Technology Topic, Popular Technical Reports.
© 2025 PatSnap. All rights reserved.Legal|Privacy policy|Modern Slavery Act Transparency Statement|Sitemap|About US| Contact US: help@patsnap.com