Preparation method of acrylic resin finishing agent modified by nano silicon dioxide (SiO2)-coated multi-walled carbon nanotubes
A technology of nano-silica and multi-walled carbon nanotubes, applied in the direction of coating, etc., can solve the problems of poor adhesion of the coating, application limitations, thermal stickiness and brittleness, etc., and achieve easy control, overcome thermal stickiness and brittleness, The effect of increasing strength
- Summary
- Abstract
- Description
- Claims
- Application Information
AI Technical Summary
Problems solved by technology
Method used
Examples
Embodiment 1
[0042] Step 1: MWCNTs / SiO 2 Preparation of:
[0043] (1) Put 0.05 parts by weight of MWCNTs-COOH in a beaker, add 43.0 parts by weight of absolute ethanol and 11.0 parts by weight of deionized water, ultrasonically disperse for 20 minutes, and transfer to a three-necked flask;
[0044](2) Under mechanical stirring, start to drop a mixed solution of 1.7 parts by weight of tetraethyl orthosilicate and 43.0 parts by weight of absolute ethanol, drop it in 2 hours, and react at room temperature for 24 hours;
[0045] (3) Add dropwise a mixed solution of 0.4 parts by weight of silane coupling agent, 1.15 parts by weight of absolute ethanol and 0.16 parts by weight of deionized water, drop it in 30 minutes, and react for another 24 hours at room temperature;
[0046] (4) Suction filter the mixed solution obtained by the reaction with a 0.22 μm microporous membrane, then wash the filter cake with ethanol, repeat several times to remove the unreacted silane coupling agent, and then dr...
Embodiment 2
[0057] Step 1: MWCNTs / SiO 2 Preparation of:
[0058] (1) Put 0.05 parts by weight of MWCNTs-COOH in a beaker, add 43.0 parts by weight of absolute ethanol and 11.0 parts by weight of deionized water, ultrasonically disperse for 20 minutes, and transfer to a three-necked flask;
[0059] (2) Under mechanical stirring, start to drop a mixed solution of 1.7 parts by weight of tetraethyl orthosilicate and 43.0 parts by weight of absolute ethanol, drop it in 2 hours, and react at room temperature for 24 hours;
[0060] (3) Add dropwise a mixed solution of 0.4 parts by weight of silane coupling agent, 1.15 parts by weight of absolute ethanol and 0.16 parts by weight of deionized water, drop it in 30 minutes, and react for another 24 hours at room temperature;
[0061] (4) Suction filter the mixed solution obtained by the reaction with a 0.22 μm microporous membrane, then wash the filter cake with ethanol, repeat several times to remove the unreacted silane coupling agent, and then d...
Embodiment 3
[0072] Step 1: MWCNTs / SiO 2 Preparation of:
[0073] (1) Put 0.05 parts by weight of MWCNTs-COOH in a beaker, add 43.0 parts by weight of absolute ethanol and 11.0 parts by weight of deionized water, ultrasonically disperse for 20 minutes, and transfer to a three-necked flask;
[0074] (2) Under mechanical stirring, start to drop a mixed solution of 1.7 parts by weight of tetraethyl orthosilicate and 43.0 parts by weight of absolute ethanol, drop it in 2 hours, and react at room temperature for 24 hours;
[0075] (3) Add dropwise a mixed solution of 0.4 parts by weight of silane coupling agent, 1.15 parts by weight of absolute ethanol and 0.16 parts by weight of deionized water, drop it in 30 minutes, and react for another 24 hours at room temperature;
[0076] (4) Suction filter the mixed solution obtained by the reaction with a 0.22 μm microporous membrane, then wash the filter cake with ethanol, repeat several times to remove the unreacted silane coupling agent, and then d...
PUM
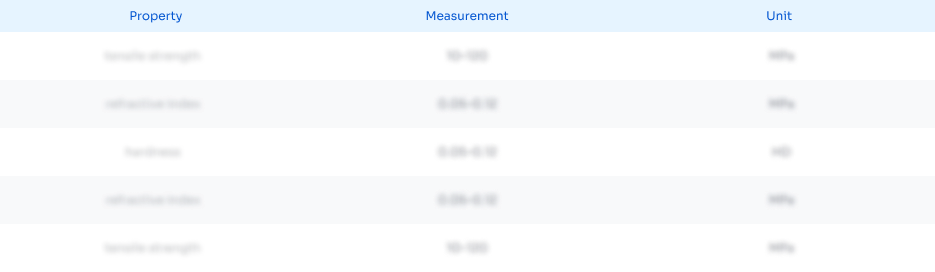
Abstract
Description
Claims
Application Information

- R&D
- Intellectual Property
- Life Sciences
- Materials
- Tech Scout
- Unparalleled Data Quality
- Higher Quality Content
- 60% Fewer Hallucinations
Browse by: Latest US Patents, China's latest patents, Technical Efficacy Thesaurus, Application Domain, Technology Topic, Popular Technical Reports.
© 2025 PatSnap. All rights reserved.Legal|Privacy policy|Modern Slavery Act Transparency Statement|Sitemap|About US| Contact US: help@patsnap.com