Method for synthesizing CPVC resin by gas-solid phase method
A chlorinated polyvinyl chloride, gas-solid phase technology, applied in the field of gas-solid phase synthesis of chlorinated polyvinyl chloride resin, can solve the problems of high cost, unsuitable for large-scale production, and many wastes
- Summary
- Abstract
- Description
- Claims
- Application Information
AI Technical Summary
Problems solved by technology
Method used
Image
Examples
Embodiment 1
[0020] This embodiment illustrates the impact of reaction time on PVC chlorination, figure 1 For the relationship between reaction time and ω(Cl), the ω(Cl) of CPVC increases with time, up to 68.14%. After more than 3 h, the trend of this change weakened, and the reaction gradually tended to balance. This is because PVC undergoes a free radical substitution reaction during chlorination, and the PVC molecular chain contains more -CH2- and -CHCl- in the initial stage of the reaction. Chlorination is faster. As the reaction proceeds, in the PVC molecular chain -CCl 2 - increases gradually, while -CH2- and -CHCl- decrease gradually, and the reaction becomes more difficult for chlorine substitution to a certain extent, and the reaction tends to be gentle at this time. Therefore, 3 h is selected as the optimal reaction time for PVC chlorine chlorination, and the ω (Cl) in the product is 67.78% at this time.
Embodiment 2
[0022] This embodiment illustrates the impact of temperature of reaction on PVC chlorination, figure 2 is the relationship between the reaction temperature and ω(Cl), by figure 2 It can be seen that the ω(Cl) of CPVC increases with the increase of the reaction temperature, but this trend weakens after reaching 112°C, and the product ω(Cl) can reach 68.65% at 125°C. This is because the reaction is an exothermic reaction, the higher the temperature, the greater the reaction resistance and the reduced reaction rate. Experiments have found that if the temperature is too high, the material will stick and turn yellow, and the reaction cannot be carried out normally. This is because CPVC with a certain ω (Cl) will degrade and de-HCl at a higher temperature. Therefore, the optimal temperature for PVC chlorination is 112°C.
Embodiment 3
[0024] This embodiment illustrates that the feed gas φ(Cl 2 ) on the impact of PVC chlorination, the chemical reaction between polymers depends on the collision probability of active groups on the polymer chain, the higher the collision probability, the easier the intermolecular reaction, and the greater the reaction rate, if φ(Cl 2 ) is too low, so that the effective collision probability of the chemical reaction is reduced. Depend on image 3 It can be seen that: φ(Cl 2 ) is less than 30%, change Cl 2 Flow has a significant effect on ω(Cl), but with φ(Cl 2 ) further increases, this effect weakens rapidly, when φ(Cl 2 ) exceeds 45%, it has little effect on the product ω(Cl). Therefore, the preferred φ(Cl 2 ) is 45%.
PUM
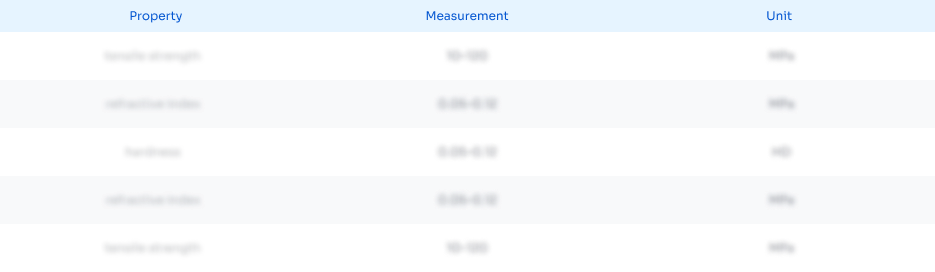
Abstract
Description
Claims
Application Information

- R&D
- Intellectual Property
- Life Sciences
- Materials
- Tech Scout
- Unparalleled Data Quality
- Higher Quality Content
- 60% Fewer Hallucinations
Browse by: Latest US Patents, China's latest patents, Technical Efficacy Thesaurus, Application Domain, Technology Topic, Popular Technical Reports.
© 2025 PatSnap. All rights reserved.Legal|Privacy policy|Modern Slavery Act Transparency Statement|Sitemap|About US| Contact US: help@patsnap.com