Recycling method of byproduct saline during preparation of hydrazine hydrate by using urea method
A technology for recycling and processing hydrazine hydrate, which is applied in the preparation of carbonate preparations, alkali metal chlorides, and bicarbonate salts, and can solve the problem of soil salinization, waste of space and resources, and unavailability of sodium chloride and sodium sulfate. and other problems to achieve the effect of improving purity and yield
- Summary
- Abstract
- Description
- Claims
- Application Information
AI Technical Summary
Problems solved by technology
Method used
Image
Examples
Embodiment 1
[0025] Get 500g of crude hydrazine solution, after testing, it contains hydrazine hydrate 50g / L, sodium chloride 220g / L, sodium carbonate 150g / L, sodium hydroxide 15g / L. Put the crude hydrazine solution into a 1L reactor, and feed carbon dioxide gas into the reactor, adjust the negative pressure of the steel cylinder containing carbon dioxide gas to 100pa, and the flow rate to be 0.8mol / L. When the negative pressure of the steel cylinder containing carbon dioxide gas is 0 , continue stirring for 0.5h. Afterwards, freeze and crystallize by circulating frozen brine, keep the temperature at 6 ° C, freeze for 2 hours, filter cold, and put the filter residue into a 35 ° C vacuum oven for drying for 4 hours. Add urea to the filtrate, add sulfuric acid to adjust the pH to 3, stir for 2 hours under the condition of controlling the temperature to be 106° C., filter to obtain biurea, and pass chlorine gas oxidation to obtain ADC foaming agent in the reactor of biurea, wherein after the ...
Embodiment 2
[0027] Get 500g thick hydrazine solution, after testing, composition is the same as above, add thick hydrazine solution in 1L reactor, and pass into carbon dioxide gas in the reactor, adjust the steel cylinder negative pressure that carbon dioxide gas is housed to be 150pa, flow rate 0.5mol / L, When the negative pressure of the steel cylinder containing carbon dioxide gas is 0, continue stirring for 0.5h. Afterwards, freeze and crystallize by circulating frozen brine, keep the temperature at 2 ° C, freeze for 2 hours, filter cold, and put the filter residue into a 45 ° C vacuum oven for drying for 4 hours. Add urea to the filtrate, add sulfuric acid to adjust the pH to 4, stir for 2 hours under the condition of controlling the temperature at 120 ° C, filter to obtain biurea, and pass chlorine gas oxidation to obtain ADC foaming agent in the biurea reaction kettle, wherein the obtained after the reaction The filtrate is sent to the electrolytic cell. The calculation shows that ...
PUM
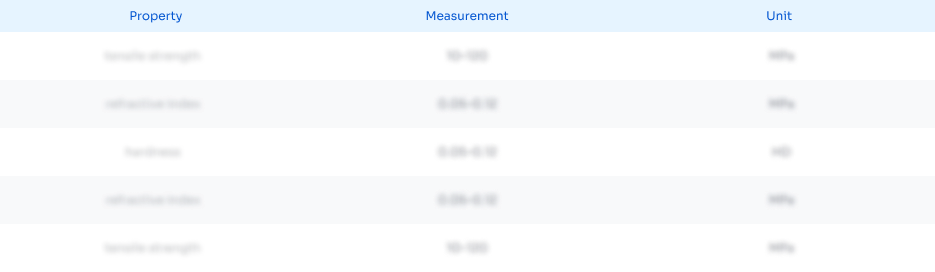
Abstract
Description
Claims
Application Information

- R&D
- Intellectual Property
- Life Sciences
- Materials
- Tech Scout
- Unparalleled Data Quality
- Higher Quality Content
- 60% Fewer Hallucinations
Browse by: Latest US Patents, China's latest patents, Technical Efficacy Thesaurus, Application Domain, Technology Topic, Popular Technical Reports.
© 2025 PatSnap. All rights reserved.Legal|Privacy policy|Modern Slavery Act Transparency Statement|Sitemap|About US| Contact US: help@patsnap.com