Preparation method of difluoroethylene carbonate
A technology of difluoroethylene carbonate and dichloroethylene carbonate, applied in the field of preparation of difluoroethylene carbonate, can solve the problem of difficult large-scale preparation of high-purity difluoroethylene carbonate, the effect is not very satisfactory, The conversion rate is not high, and the reaction time is shortened, the reaction conditions are mild, and the selectivity is improved.
- Summary
- Abstract
- Description
- Claims
- Application Information
AI Technical Summary
Problems solved by technology
Method used
Image
Examples
Embodiment 1
[0026] Under the protection of nitrogen, add 1Kg anhydrous potassium fluoride, 1.6L acetonitrile, 20g tetrakis (diethylamino) phosphorus bromide to the 5000ml tetrafluoro reactor, after connecting the condenser vent pipe and other devices, start stirring, Stir vigorously, turn on the heating, raise the temperature to 70°C, then add 800g of dichloroethylene carbonate dropwise with a constant pressure funnel for 2 hours, after the addition, keep warm for 3 hours, cool down and filter, and wash the filter residue twice with 400ml of acetonitrile , Obtain filtrate 1.98Kg. Neutralize the filtrate with a saturated sodium bicarbonate solution, separate the organic phase, dry with anhydrous magnesium sulfate for 24 hours, filter, and transfer the resulting filtrate to a distillation apparatus for distillation under reduced pressure. After the distillation ends, 525 g of the product difluoroethylene carbonate is obtained. , GC content is 88.65%. Further rectification and purification ...
Embodiment 2
[0028] Under the protection of nitrogen, add 1Kg anhydrous potassium fluoride, 1.6L α-pyrrolidone, 30g tetrakis(diethylamino)phosphorus bromide into the 5000ml tetrafluoro reactor, and after connecting the condenser vent pipe and other devices, open the Stir, turn on the heating, raise the temperature to 90°C, then add 800g of dichloroethylene carbonate dropwise with a constant pressure funnel for 2 hours, after the dropwise addition, keep warm for 2.5 hours, cool down and filter, and wash the filter residue with 400ml α-pyrrolidone 2 times, the filtrate 2.2Kg was obtained. Neutralize the filtrate with a saturated sodium bicarbonate solution, separate the organic phase, dry with anhydrous magnesium sulfate for 24 hours, filter, and transfer the resulting filtrate to a distillation apparatus for distillation under reduced pressure. After the distillation ends, 485g of the product difluoroethylene carbonate is obtained. , the GC content is 86.87%.
Embodiment 3
[0030] Under nitrogen protection, add 1Kg of anhydrous potassium fluoride, 1.6L of γ-butyrolactone, and 35g of tetrakis(diethylamino)phosphorus bromide into a 5000ml tetrafluoro reactor, and connect the condenser vent pipe and other devices. , start stirring, turn on heating, heat up to 85°C, then add 800g of dichloroethylene carbonate dropwise with a constant pressure funnel, dropwise for 2 hours, after the addition, heat up to 100°C, keep warm for 2.5 hours, cool down and filter and use 400ml of γ-butyrolactone washed the filter residue twice to obtain 2.3Kg of filtrate. Neutralize the filtrate with a saturated sodium bicarbonate solution, separate the organic phase, dry with anhydrous magnesium sulfate for 24 hours, filter, and transfer the resulting filtrate to a distillation apparatus for vacuum distillation. After the distillation ends, 468g of the product difluoroethylene carbonate is obtained. , GC content is 87.05%.
PUM
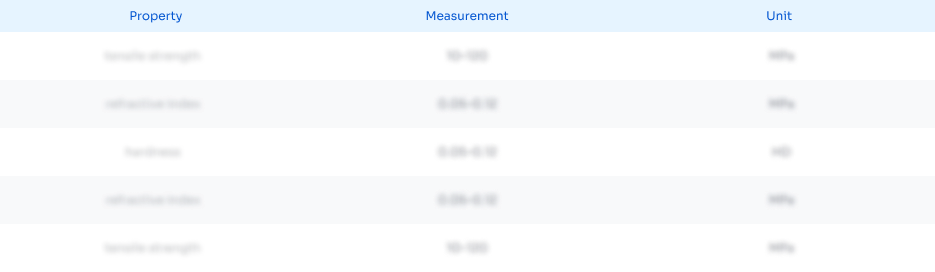
Abstract
Description
Claims
Application Information

- Generate Ideas
- Intellectual Property
- Life Sciences
- Materials
- Tech Scout
- Unparalleled Data Quality
- Higher Quality Content
- 60% Fewer Hallucinations
Browse by: Latest US Patents, China's latest patents, Technical Efficacy Thesaurus, Application Domain, Technology Topic, Popular Technical Reports.
© 2025 PatSnap. All rights reserved.Legal|Privacy policy|Modern Slavery Act Transparency Statement|Sitemap|About US| Contact US: help@patsnap.com