Preparation method for transference resistance leather dye
A migration-resistant, leather-based technology that is applied in dyeing, organic dyes, textiles, and papermaking. It can solve the problems of poor color fastness of leather, casein resistance to light, and migration resistance, and achieve good color and transparency. , easy control of functionality, and stable performance of dyes
- Summary
- Abstract
- Description
- Claims
- Application Information
AI Technical Summary
Problems solved by technology
Method used
Examples
preparation example Construction
[0031] The technical process of the preparation of the anti-migration leather polymer dye of the present invention is as follows:
[0032] Add metered isocyanates, polyols and catalysts into the reactor, wherein the molar ratio of isocyanates to polyols is 1:0.10 to 0.50, preferably 1:0.15 to 0.45, and the catalyst is 0.02% to 0.02% of the total weight of isocyanates, polyols and reactive dyes 0.06%, preferably 0.03%~0.05%, stirring reaction at 60~90°C for 60~180min, preferably 70~80°C, 90~130min, to generate polyurethane prepolymer; The total weight of polyols and reactive dyes is 50% to 100%; when reactive dyes are added, the molar ratio of isocyanate to reactive dyes is 1:0.65 to 0.90, preferably 1:0.70 to 0.80, and the reaction is stirred at 60 to 95°C for 60 to 180 minutes , preferably 75-90°C, 90-150min; adding a chain extender, the molar ratio of isocyanate to chain extender is 1:0.10-0.60, preferably 1:0.20-0.50, and the hydroxyl-containing chain extender reacts at 70-95...
Embodiment 1
[0035] Add 672.8kg HDI, 2000kg polypropylene glycol 2000, 2.01kg dibutyltin dilaurate to the reaction kettle, stir and react at 75°C for 120min to form a polyurethane prepolymer; add 4000kg N, N-dimethylformamide and stir evenly; add 1145.5kg Reactint-Black X41LV (hydroxyl value: 137), react at 90°C for 120min, then add 212.7kg of hexanediol, react at 80°C for 60min; then add 2515kg N,N-dimethylformamide dropwise to obtain a solid content of 38.22 % of migration resistant leather dyes.
Embodiment 2
[0037] Add 1111.5kg of IPDI, 1500kg of polypropylene glycol 1500, and 1.71kg of dibutyltin dilaurate into the reaction kettle, and stir and react at 80°C for 90 minutes to form a polyurethane prepolymer; add 3500kg of tetrahydrofuran and stir evenly; add 1468.9kg of reactint-red X64 (Hydroxyl value: 180), react at 80°C for 150min, then add 188.5kg of 2-aminoethylethanolamine, react at 75°C for 50min; add dropwise 3000kg of tetrahydrofuran to obtain a migration-resistant leather dye with a solid content of 39.64%.
PUM
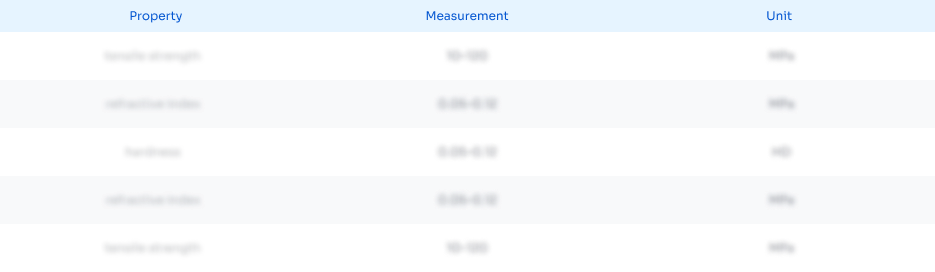
Abstract
Description
Claims
Application Information

- R&D
- Intellectual Property
- Life Sciences
- Materials
- Tech Scout
- Unparalleled Data Quality
- Higher Quality Content
- 60% Fewer Hallucinations
Browse by: Latest US Patents, China's latest patents, Technical Efficacy Thesaurus, Application Domain, Technology Topic, Popular Technical Reports.
© 2025 PatSnap. All rights reserved.Legal|Privacy policy|Modern Slavery Act Transparency Statement|Sitemap|About US| Contact US: help@patsnap.com