Bundle of roving yarns, method of manufacturing a bundle of roving yarns and method for manufacturing a work piece
A thick yarn and yarn technology, applied in the field of manufacturing workpieces, can solve the problems of multi-labor and high cost of final products, and achieve the effects of rapid productivity, improved orientation of linear fibers, and rapid impregnation.
- Summary
- Abstract
- Description
- Claims
- Application Information
AI Technical Summary
Problems solved by technology
Method used
Image
Examples
Embodiment Construction
[0040] now refer to Figure 1-6 A first embodiment of the present invention will be described. figure 1 The method of the present invention for producing a roving bundle is schematically shown. A plurality of roving yarns 1 and a central resin flowing yarn 2 are assembled into a roving bundle 5 by means of a winding device 4 . The additional winding yarn 3 is wound circumferentially around a roving bundle 5 by means of a winding device 4 .
[0041] The rovings 1 may comprise glass fibres, carbon fibres, basalt fibres, aramid fibers or natural fibers, for example fibers from wood or plants. Roving yarn 1 comprises longitudinal unidirectional reinforcing fibers. The bundle 5 preferably comprises at least 10, advantageously 10-100 roving yarns 1 . The wrapping yarn 3 may advantageously be an elastic yarn. This causes the bundles 5 to change their circular shape when placed in the mould, allowing all the bundles 5 to fit without air gaps between the bundles. However, it is c...
PUM
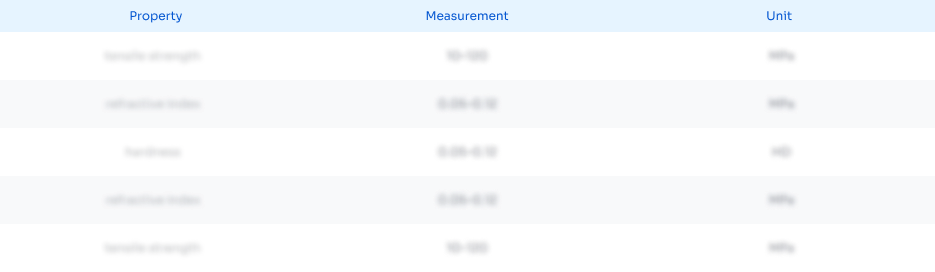
Abstract
Description
Claims
Application Information

- R&D
- Intellectual Property
- Life Sciences
- Materials
- Tech Scout
- Unparalleled Data Quality
- Higher Quality Content
- 60% Fewer Hallucinations
Browse by: Latest US Patents, China's latest patents, Technical Efficacy Thesaurus, Application Domain, Technology Topic, Popular Technical Reports.
© 2025 PatSnap. All rights reserved.Legal|Privacy policy|Modern Slavery Act Transparency Statement|Sitemap|About US| Contact US: help@patsnap.com