Papermaking method by oxidizing banana stemfiber
A banana stem and fiber technology, applied in the post-treatment of cellulose pulp, papermaking, textiles and papermaking, etc., to achieve the effects of high yield, good fiber quality, and increased pulp yield
- Summary
- Abstract
- Description
- Claims
- Application Information
AI Technical Summary
Problems solved by technology
Method used
Image
Examples
Embodiment 1
[0016] 1. Slicing:
[0017] 1000 kilograms of fresh banana stalks after harvesting are collected and cut into 5 × 7 cm slices with a slicer, and then the sheet-shaped stalks are roughly ground into fiber slurry with a coarse grinder for pulping in a paper mill.
[0018] 2. Washing:
[0019] After being transported to a continuous hydropulper with a volume of 5 cubic meters by a screw machine for cleaning, it flows into a vibrating screen with an aperture of 6 mm for washing, and the hemicellulose, lignin and pectin are washed away by washing.
[0020] 3. Squeeze:
[0021] After washing, an extruder is used to extrude the fiber slurry with a water content of 50-60%.
[0022] 4. Oxidation:
[0023] Put the extruded fiber slurry into a circular carbon steel container with a volume of 5 cubic meters, add 10 kg of quicklime with a pH value of 7-8, and stir for 20-30 minutes. At the same time, slowly add sodium hypochlorite with a content of 85% to 5-7% of the quality of the fib...
Embodiment 2
[0027] 1. Slicing: Collect 2,000 kg of fresh banana stems after harvesting and cut them into 5×7cm slices with a slicer, and then use the coarse grinder used in paper mills to roughly grind the sliced stems into fiber pulp material;
[0028] 2. Washing:
[0029] After being transported to a continuous hydropulper with a volume of 5 cubic meters by a screw machine for cleaning, it flows into a vibrating screen with an aperture of 6 mm for washing, and the hemicellulose, lignin and pectin are washed away by washing.
[0030] 3. Squeeze:
[0031] After washing, an extruder is used to extrude the fiber slurry with a water content of 50-60%.
[0032] 4. Oxidation:
[0033] Put the extruded fiber slurry into a circular carbon steel container with a volume of 5 cubic meters, add 20 kg of quicklime with a pH value of 7-8, and stir for 20-30 minutes. At the same time, slowly add sodium hypochlorite with a content of 85% to 5-7% of the quality of the fiber slurry with a water cont...
Embodiment 3
[0037] 1. Slicing:
[0038] Collect 5,000 kilograms of banana stems after harvesting and cut them into 5×7cm slices with a slicer, and then coarsely grind the sliced banana stems with a coarse grinder commonly used in paper mills for pulping.
[0039] 2. Washing:
[0040] After being transported to a continuous hydropulper with a volume of 5 cubic meters by a screw machine for cleaning, it flows into a vibrating screen with an aperture of 6 mm for washing, and the hemicellulose, lignin and pectin are washed away by washing.
[0041] 3. Squeeze:
[0042] After washing, an extruder is used to extrude the fiber slurry with a water content of 50-60%.
[0043] 4. Oxidation:
[0044] Put the extruded fiber slurry into a circular carbon steel container with a volume of 5 cubic meters, add 50 kg of quicklime with a pH value of 7-8, and stir for 20-30 minutes. At the same time, slowly add sodium hypochlorite with a content of 85% to 5-7% of the quality of the fiber slurry with a ...
PUM
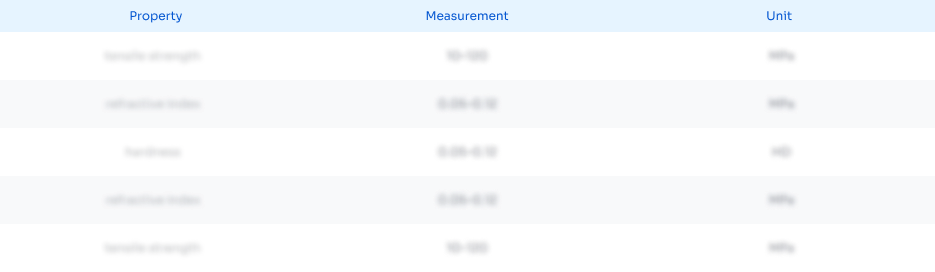
Abstract
Description
Claims
Application Information

- R&D
- Intellectual Property
- Life Sciences
- Materials
- Tech Scout
- Unparalleled Data Quality
- Higher Quality Content
- 60% Fewer Hallucinations
Browse by: Latest US Patents, China's latest patents, Technical Efficacy Thesaurus, Application Domain, Technology Topic, Popular Technical Reports.
© 2025 PatSnap. All rights reserved.Legal|Privacy policy|Modern Slavery Act Transparency Statement|Sitemap|About US| Contact US: help@patsnap.com