Vanadium and titanium compound microalloyed steel bar and production method thereof
A microalloying and alloying technology, applied in the field of microalloying of iron and steel metallurgy, to achieve the effect of improving yield strength and tensile strength, low production cost, and high solid solution strengthening effect
- Summary
- Abstract
- Description
- Claims
- Application Information
AI Technical Summary
Problems solved by technology
Method used
Image
Examples
preparation example Construction
[0034] The preparation method of the above-mentioned vanadium-titanium composite microalloyed steel bar comprises the following steps:
[0035] a. Smelt steelmaking raw materials into crude steel liquid, tap steel, and carry out deoxidation and alloying during the tapping process;
[0036]b. The molten steel after tapping is sent to the refining furnace for refining and composition fine-tuning, so that it meets the requirements of the steel bar composition and then casts to obtain a steel billet for rolling steel bars;
[0037] c. Heat the rolled steel billet to 1100-1300°C and keep it warm for 30-150 minutes, then roll it, and finish rolling when it reaches 750-950°C, and air-cool the rolled steel bar to room temperature to obtain vanadium-titanium Composite microalloyed steel bars;
[0038] Among them, the alloying of vanadium and titanium is performed during the tapping process and after deoxidation, or during the refining process.
[0039] The invention strictly controls...
Embodiment 1
[0049] (1) To produce HRB400 steel bar with slag iron as raw material, through slag making, oxygen blowing and other measures, it is smelted into crude molten steel through electric furnace. Crude molten steel contains [C]0.13%, [P]0.019%, [S]0.070%, [N]67ppm, a[o]68ppm, temperature 1678°C, meet the specified requirements, and then tap the steel, deoxidation alloying is carried out during the tapping process, vanadium and titanium pass through the block Ti-23wt%Si-26wt% with a particle size of 25mm Fe and V-25wt% Fe are added in the form of master alloys, and the deoxidized and alloyed molten steel is sent to LF furnace for refining and composition fine-tuning, and the obtained molten steel is sent to billet continuous casting. The composition is shown in Table 1.
[0050] (2) Heat the billet to 1200°C for 1 hour.
[0051] (3) Air-cool or water-cool the above-mentioned heated slab to 1030°C, and then carry out rolling, and the final rolling temperature is 820°C.
[0052] (4) ...
Embodiment 2
[0055] (1) Using slag steel as raw material to produce HRB400 steel bars, smelting into crude steel through electric furnace through slag making, oxygen blowing and other measures, the composition contains [C]0.17%, [P]0.020%, [S]0.080%, [N ]63ppm, a[o]65ppm, the temperature reaches 1685°C and meets the specified requirements, and then the steel is tapped, and deoxidation alloying is carried out during the tapping process. Titanium is respectively added in the form of Ti-45wt%Si-10wt%Fe cored wire, vanadium The content is the residual amount in slag steel. The molten steel after deoxidation and alloying is sent to LF furnace for refining and composition fine-tuning, and the obtained molten steel is sent to billet continuous casting. The composition is shown in Table 1.
[0056] (2) Heat the billet to 1230°C for 1 hour.
[0057] (3) Air-cool or water-cool the above-mentioned heated slab to 1050°C, and then carry out rolling, and the final rolling temperature is 850°C.
[0058]...
PUM
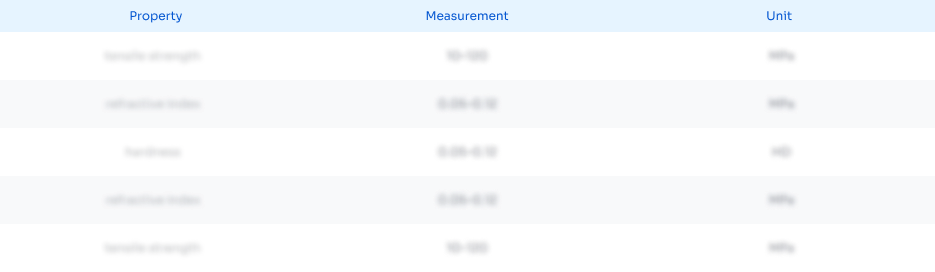
Abstract
Description
Claims
Application Information

- Generate Ideas
- Intellectual Property
- Life Sciences
- Materials
- Tech Scout
- Unparalleled Data Quality
- Higher Quality Content
- 60% Fewer Hallucinations
Browse by: Latest US Patents, China's latest patents, Technical Efficacy Thesaurus, Application Domain, Technology Topic, Popular Technical Reports.
© 2025 PatSnap. All rights reserved.Legal|Privacy policy|Modern Slavery Act Transparency Statement|Sitemap|About US| Contact US: help@patsnap.com