Heat treatment process of hot-work-die steel for aluminum die-casting mould
A hot work die steel and process technology, applied in the field of iron and steel metallurgy technology, can solve problems such as cracks and increased thermal stress of water-cooled holes, and achieve the effects of optimized design, guaranteed hardness, and good thermal crack resistance.
- Summary
- Abstract
- Description
- Claims
- Application Information
AI Technical Summary
Problems solved by technology
Method used
Examples
Embodiment 1
[0022] A heat treatment process for hot work die steel, the hot work die steel is composed of the following components in weight percentage: C 0.30%, Si 1.20%, Mn 1.50%, Cr 5.50%, W 1.60%, Mo 0.30%, V 1.60%, Ni 1.60%, Co 0.2%, Nb 0.7%, S≤0.005%, P≤0.03%, and the balance is Fe; the heat treatment process includes the following steps:
[0023] (1) Quenching: Heat the mold steel billet to 650°C at a heating rate of 60°C / min, and keep it for 90 minutes; then heat it to 1080°C at a heating rate of 60°C / min, hold it for 180 minutes, and cool it by oil quenching;
[0024] (2) Tempering: For the first tempering, heat up to 500°C at a heating rate of 60°C / min, then air cool to room temperature, temper for the second time, and heat to 450°C at a heating rate of 30°C / min, then Air cool to room temperature.
Embodiment 2
[0026] A heat treatment process for hot work die steel, the hot work die steel is composed of the following components in weight percentage: C 0.50%, Si 0.80%, Mn 1.70%, Cr 4.50%, W 2.00%, Mo 0.10%, V 1.80%, Ni 1.20%, Co 0.4%, Nb 0.5%, S≤0.005%, P≤0.03%, and the balance is Fe; the heat treatment process includes the following steps:
[0027] (1) Quenching: Heat the mold steel billet to 630°C at a heating rate of 90°C / min, and keep it for 120 minutes; then heat it to 1120°C at a heating rate of 30°C / min, hold it for 150 minutes, and cool it by oil quenching;
[0028] (2) Tempering: For the first tempering, heat up to 480°C at a heating rate of 90°C / min, then air cool to room temperature, temper for the second time, and heat to 430°C at a heating rate of 60°C / min, then Air cool to room temperature.
Embodiment 3
[0030] A heat treatment process for hot work die steel, the hot work die steel is composed of the following components in weight percentage: C 0.40%, Si 1.0%, Mn 1.60%, Cr 5.0%, W 1.8%, Mo 0.20%, V 1.7%, Ni 1.4%, Co 0.3%, Nb 0.6%, S≤0.005%, P≤0.03%, the rest is Fe;
[0031] Described heat treatment process comprises the following steps:
[0032] (1) Quenching: Heat the die steel billet to 640°C at a heating rate of 75°C / min, and keep it for 105 minutes; then heat it to 1100°C at a heating rate of 45°C / min, hold it for 165 minutes, and cool it by oil quenching;
[0033] (2) Tempering: For the first tempering, heat up to 490°C at a heating rate of 75°C / min, then air cool to room temperature, temper for the second time, and heat to 440°C at a heating rate of 45°C / min, then Air cool to room temperature.
PUM
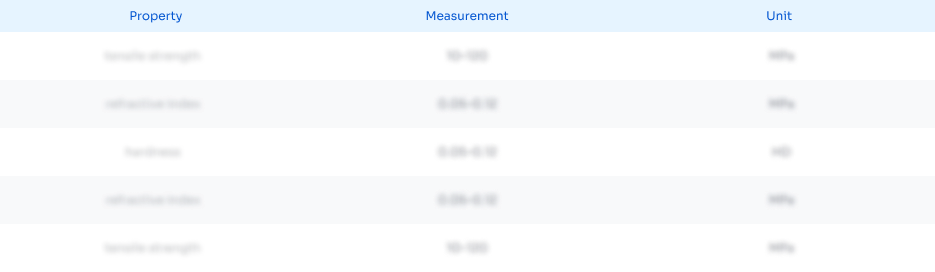
Abstract
Description
Claims
Application Information

- R&D
- Intellectual Property
- Life Sciences
- Materials
- Tech Scout
- Unparalleled Data Quality
- Higher Quality Content
- 60% Fewer Hallucinations
Browse by: Latest US Patents, China's latest patents, Technical Efficacy Thesaurus, Application Domain, Technology Topic, Popular Technical Reports.
© 2025 PatSnap. All rights reserved.Legal|Privacy policy|Modern Slavery Act Transparency Statement|Sitemap|About US| Contact US: help@patsnap.com