Fireproof coating primer of single-mass-system indoor thin steel structure
A technology for fire-resistant coatings and steel structures, applied in fire-resistant coatings, coatings, etc., can solve the problems of mildew in emulsions, low labor productivity, increased production, packaging, and transportation costs, and achieve high-temperature mildew and simplified production process, the effect of shortening the mixing time
- Summary
- Abstract
- Description
- Claims
- Application Information
AI Technical Summary
Problems solved by technology
Method used
Image
Examples
Embodiment 1
[0029] Add 6.8 parts by mass of styrene-acrylic rubber powder and 2.2 parts by mass of VAE rubber powder into a dry powder mixer and start stirring, then add 0.1 parts by mass of dispersant, 0.2 parts by mass of defoamer, 14.5 parts by mass of ammonium polyphosphate, and 4.8 parts by mass of melamine. 4.7 parts by mass of pentaerythritol, 16 parts by mass of floating beads, 4 parts by mass of mineral wool, and 0.02 parts by mass of polypropylene fiber, stirred and mixed for 10-15 minutes, and fully mixed to obtain a finished product. According to the finished product: water = 1.0:0.4, mix well, spray on the 70×150×6 (mm) steel plate that has been coated with anti-rust paint for curing, the curing period is 15 days, the ambient temperature is between 0~38°C, and the relative humidity is less than 85 %. After the curing period expired, its performance was measured, and the results are shown in Table 1 below.
Embodiment 2
[0031] Put 7.5 parts by mass of styrene-acrylic rubber powder and 2.5 parts by mass of VAE rubber powder into a dry powder mixer and start stirring, then add 0.15 parts by mass of dispersant, 0.20 parts by mass of defoamer, 15 parts by mass of ammonium dihydrogen phosphate, and 5 parts by mass of urea Parts, 5 parts by mass of monopentaerythritol, 16 parts by mass of floating beads, 5 parts by mass of fly ash, 0.01 part by mass of glass fiber, and 0.02 part by mass of polypropylene fiber. Stir and mix for 10-15 minutes, and mix thoroughly to obtain the finished product. After fully mixing the dry ingredients, add water at a ratio of 1.0:0.4 and mix evenly. Spraying boards, curing conditions are the same as in Example 1, and its performance is measured after the curing period expires. The results are shown in Table 1.
Embodiment 3
[0033] Put 8.3 parts by mass of styrene-acrylic rubber powder and 2.8 parts by mass of VAE rubber powder into the dry powder mixer and start stirring, then add 0.20 parts by mass of dispersant, 0.25 parts by mass of defoamer, 15.6 parts by mass of diammonium hydrogen phosphate, and dicyandiamide 5.2 parts by mass, 5.2 parts by mass of dipentaerythritol, 18 parts by mass of floating beads, 4 parts by mass of expandable graphite, and 0.03 parts by mass of glass fiber. Stir and mix for 15-20 minutes, and mix thoroughly to obtain the finished product. After fully mixing the dry material, add water at a ratio of 1.0:0.4 to mix and spray to make boards. The curing conditions are the same as in Example 1. After the curing period expires, test its performance.
PUM
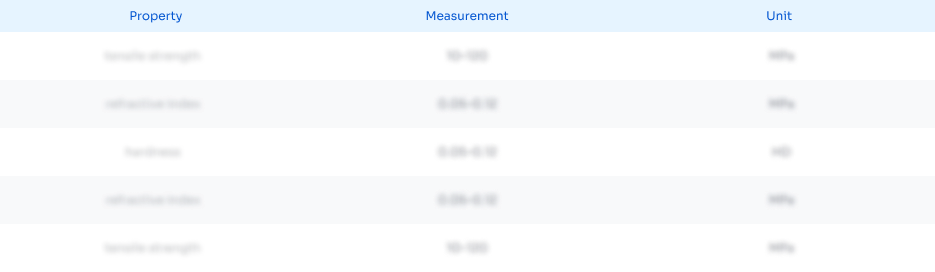
Abstract
Description
Claims
Application Information

- R&D Engineer
- R&D Manager
- IP Professional
- Industry Leading Data Capabilities
- Powerful AI technology
- Patent DNA Extraction
Browse by: Latest US Patents, China's latest patents, Technical Efficacy Thesaurus, Application Domain, Technology Topic, Popular Technical Reports.
© 2024 PatSnap. All rights reserved.Legal|Privacy policy|Modern Slavery Act Transparency Statement|Sitemap|About US| Contact US: help@patsnap.com