Preparation method of carbon nanotube/thermosetting resin composite material
A technology of resin composite materials and carbon nanotubes, which is applied in the field of preparation of organic polymer compounds, can solve the problems of dielectric loss, waste of energy, high dielectric constant, and high dielectric loss, so as to reduce the probability of conductive paths and increase the generation of probability, the effect of low dielectric loss
- Summary
- Abstract
- Description
- Claims
- Application Information
AI Technical Summary
Problems solved by technology
Method used
Image
Examples
Embodiment 1
[0023] 0.02 g of multi-walled carbon nanotubes and 20 g of bisphenol A cyanate were mixed, ultrasonically oscillated and stirred at 85° C. for 1 hour to obtain a mixed solution, and then the mixed solution was prepolymerized at 150° C. for 2 hours. After the prepolymerization was finished, the prepolymer was divided into 2 equal parts. Pour one part of it into a preheated mold, and vacuum defoam at 140°C for 30 minutes. Then put the mold into an oven, pre-cure at 180° C. for 30 minutes, and obtain a carbon nanotube / cyanate resin composite material pre-cured sheet after cooling.
[0024] Cast the remaining 1 part of prepolymer on the precured sheet, after vacuum defoaming at 140°C for 30min, perform curing and post-treatment according to the process 180°C / 2h+200°C / 2h+220°C / 2h and 240°C / 4h , to obtain carbon nanotube / cyanate resin composite material.
Embodiment 2
[0026] Mix 0.4 g of single-walled carbon nanotubes and 20 g of bisphenol A cyanate, and ultrasonically vibrate and stir at 85° C. for 1 hour to obtain a mixed solution, and then prepolymerize the mixed solution at 150° C. for 2 hours. After the prepolymerization, divide the prepolymer into 3 parts with a mass ratio of 2:1:1. Pour one part of it into a preheated mold, and vacuum defoam at 140°C for 30 minutes. Then put the mold into an oven, pre-cure at 180° C. for 30 minutes, and obtain a carbon nanotube / cyanate resin composite material pre-cured sheet A after cooling.
[0027] The second part of prepolymer was poured on the above-mentioned pre-cured sheet A, vacuum defoamed at 140°C for 30 minutes, and the carbon nanotube / cyanate resin composite material pre-cured sheet B was obtained after cooling.
[0028] Cast the third part of the prepolymer on the precured sheet B, and after vacuum degassing at 140°C for 30 minutes, cure and post-cure according to the process 180°C / 2h+2...
Embodiment 3
[0030] 0.14 g of single-walled carbon nanotubes and 20 g of bisphenol A cyanate were mixed, ultrasonically oscillated and stirred at 85° C. for 1 hour to obtain a mixed solution, and then the mixed solution was prepolymerized at 150° C. for 2 hours. After the prepolymerization, divide the prepolymer into 4 parts with a mass ratio of 2:1:2:1. Pour one part of it into a preheated mold, and vacuum defoam at 140°C for 30 minutes. Then put the mold into an oven, pre-cure at 180° C. for 30 minutes, and obtain a carbon nanotube / cyanate resin composite material pre-cured sheet A after cooling.
[0031] The second part of prepolymer was poured on the above-mentioned pre-cured sheet A, vacuum defoamed at 140°C for 30 minutes, and the carbon nanotube / cyanate resin composite material pre-cured sheet B was obtained after cooling.
[0032] The third part of prepolymer was poured on the pre-cured sheet B above, vacuum degassed at 140° C. for 30 minutes, and the carbon nanotube / cyanate resin...
PUM
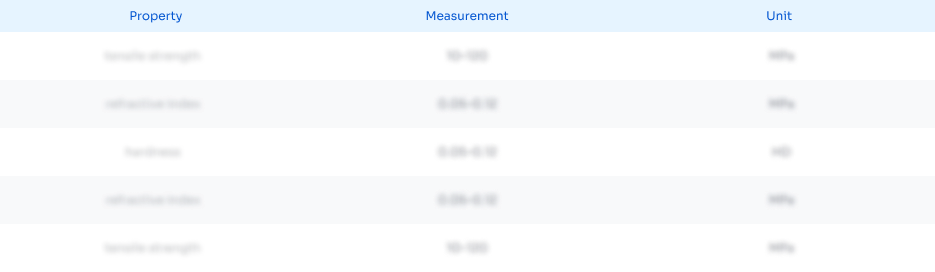
Abstract
Description
Claims
Application Information

- R&D
- Intellectual Property
- Life Sciences
- Materials
- Tech Scout
- Unparalleled Data Quality
- Higher Quality Content
- 60% Fewer Hallucinations
Browse by: Latest US Patents, China's latest patents, Technical Efficacy Thesaurus, Application Domain, Technology Topic, Popular Technical Reports.
© 2025 PatSnap. All rights reserved.Legal|Privacy policy|Modern Slavery Act Transparency Statement|Sitemap|About US| Contact US: help@patsnap.com