Precision five-axis double-station position changing machine
A dual-station, positioner technology, applied in the direction of manufacturing tools, metal processing equipment, auxiliary devices, etc., can solve problems such as reducing production efficiency, improve production efficiency, save production time, rotation accuracy and repeat positioning accuracy high effect
- Summary
- Abstract
- Description
- Claims
- Application Information
AI Technical Summary
Problems solved by technology
Method used
Image
Examples
Embodiment 1
[0020] Embodiment one: see attached figure 1 to attach Figure 4 shown.
[0021] A precision five-axis double-station positioner for assisting automatic welding. The precision five-axis double-station positioner includes a rotary base 1, a column box 2 mounted on the rotary base 1 that can rotate horizontally, a first servo motor 3 that drives the column box 2 to rotate, and a column box that is oppositely arranged 2 The first clamping device 4 and the second clamping device 5 on both sides, and the middle part of the column box 2 is provided with an arc protection screen 6 separating the first clamping device 4 and the second clamping device 5 .
[0022] The first clamping device 4 includes a first rocker arm 7 in the shape of "冂", a second servo motor 8 that connects the column box 2 and the first rocker arm 7 and drives the first rocker arm 7 to rotate vertically, and the relative arrangement The first headstock 9 and the first tailstock 10 at both ends of the first rock...
PUM
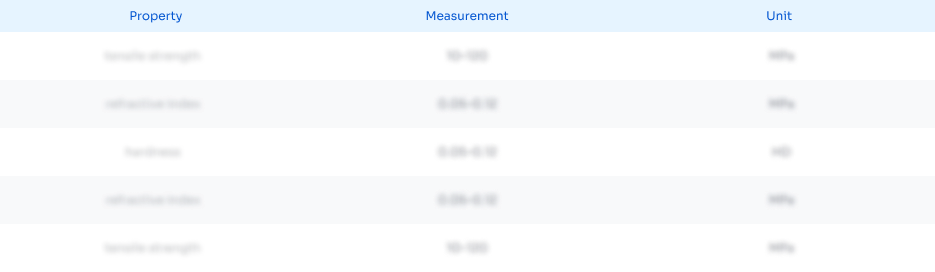
Abstract
Description
Claims
Application Information

- R&D
- Intellectual Property
- Life Sciences
- Materials
- Tech Scout
- Unparalleled Data Quality
- Higher Quality Content
- 60% Fewer Hallucinations
Browse by: Latest US Patents, China's latest patents, Technical Efficacy Thesaurus, Application Domain, Technology Topic, Popular Technical Reports.
© 2025 PatSnap. All rights reserved.Legal|Privacy policy|Modern Slavery Act Transparency Statement|Sitemap|About US| Contact US: help@patsnap.com