Para-hydroxybenzoic acid continuous production technique by liquid-phase method
A p-hydroxybenzoic acid, production process technology, applied in the direction of carboxylate preparation, chemical instruments and methods, sulfate/bisulfate preparation, etc., can solve the problem that phenol-containing wastewater is difficult to treat, and achieve easy control of reaction temperature, The effect of shortening the reaction time and increasing the operating flexibility
- Summary
- Abstract
- Description
- Claims
- Application Information
AI Technical Summary
Problems solved by technology
Method used
Image
Examples
Embodiment 1
[0029] Embodiment 1: the production technique of p-hydroxybenzoic acid of the present invention adopts phenol and potassium hydroxide to carry out salification reaction, carries out carboxylation reaction with carbon dioxide after salt formation, finally obtains p-hydroxybenzoic acid product with concentrated sulfuric acid acid analysis; The continuation on the technology has been reduced, and the pollution and waste in the production process have been reduced. The technical process of the present invention comprises: reaction process, filtration process, extraction recovery process, potassium sulfate production process, and concrete technical process is as follows:
[0030] (1) Reaction process
[0031] Mix 50% potassium hydroxide solution, phenol, kerosene and isooctyl alcohol in a certain proportion, the mass ratio is 1:1:2, and the mass ratio of kerosene to isooctyl alcohol is 4:1, put it into the salt-forming reactor, and heat it at 120°C Perform a salt-forming reaction a...
Embodiment 2
[0044] (1) Reaction process
[0045] Mix 50% potassium hydroxide solution, phenol, kerosene and isooctyl alcohol in a certain proportion, the mass ratio is 1:2.5:10, the mass ratio of kerosene to isooctyl alcohol is 2.5:1, put it into the salt-forming reactor, and heat it at 180°C Perform a salt-forming reaction at left and right under normal pressure to obtain potassium phenate;
[0046] Transfer the above materials into the carboxylation reactor, and feed carbon dioxide until the carboxylation is completed, control the temperature at 230°C, and the pressure at 0.6MPa, and the reaction ends after about 4 hours;
[0047] After the carboxylation reaction is finished, add desalted water to the material to obtain an aqueous solution of potassium p-potassium oxybenzoate, unreacted phenol and solvent are recycled back to the salt-forming reaction kettle, and the separation process is realized by phase separation in a phase separation tower.
[0048] Add activated carbon in potassi...
Embodiment 3
[0058] (1) Reaction process
[0059] Mix 50% potassium hydroxide solution, phenol, kerosene and isooctyl alcohol in a certain proportion, the mass ratio is 1:3.5:20, the mass ratio of kerosene to isooctyl alcohol is 1:1, put it into the salt-forming reactor, and heat it at 220°C Perform a salt-forming reaction at left and right under normal pressure to obtain potassium phenate;
[0060] Transfer the above materials into the carboxylation reactor, and feed carbon dioxide until the carboxylation is completed, control the temperature at 260°C, and the pressure at 0.8MPa, and the reaction ends after about 4 hours;
[0061] After the carboxylation reaction is finished, add desalted water to the material to obtain an aqueous solution of potassium p-potassium oxybenzoate, unreacted phenol and solvent are recycled back to the salt-forming reaction kettle, and the separation process is realized by phase separation in a phase separation tower.
[0062] Add gac in the aqueous solution o...
PUM
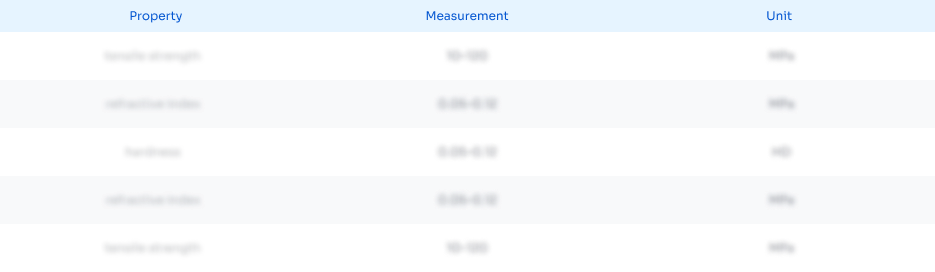
Abstract
Description
Claims
Application Information

- Generate Ideas
- Intellectual Property
- Life Sciences
- Materials
- Tech Scout
- Unparalleled Data Quality
- Higher Quality Content
- 60% Fewer Hallucinations
Browse by: Latest US Patents, China's latest patents, Technical Efficacy Thesaurus, Application Domain, Technology Topic, Popular Technical Reports.
© 2025 PatSnap. All rights reserved.Legal|Privacy policy|Modern Slavery Act Transparency Statement|Sitemap|About US| Contact US: help@patsnap.com