Environment-friendly flame-retardant polyvinyl chloride cable insulating material and preparation method thereof
A technology for flame-retardant polyvinyl chloride and cable insulation, which is applied in the direction of organic insulators, plastic/resin/wax insulators, etc., and can solve problems such as toxic and corrosive fumes, fire fighting, and loss of people's lives and property
- Summary
- Abstract
- Description
- Claims
- Application Information
AI Technical Summary
Problems solved by technology
Method used
Image
Examples
Embodiment 1
[0022] First put (the following are parts by weight) 100 parts of polyvinyl chloride and 6 parts of stabilizer into a high-speed mixer for high-speed mixing. When the temperature rises to 60°C, add 40 parts of plasticizer UN488, 6 parts of long-chain chlorine Chemical paraffin and 4 parts of epoxidized soybean oil, when the temperature reaches 80°C, add 5 parts of antimony trioxide, 8 parts of hydrated zinc borate, and 12 parts of activated aluminum hydroxide, when the temperature reaches 90°C, add 10 parts of calcined Kaolin, 15 parts of heavy calcium carbonate and 20 parts of nano calcium carbonate, when the temperature reaches 100 ° C, add 0.6 parts of stearic acid and 0.6 parts of butyl stearate, when the temperature reaches 110 ° C, stop high-speed mixing. Unload the material into the low-speed mixer for low-speed mixing and cooling, unload the cooled material into the hopper elevator, add it to the twin-screw extruder for mixing, extrude, granulate and pack.
Embodiment 2
[0024] First put (the following are parts by weight) 100 parts of polyvinyl chloride and 5 parts of stabilizer into a high-speed mixer for high-speed mixing. When the temperature rises to 60°C, add 35 parts of plasticizer UN488, 4 parts of long-chain chlorine Chemical paraffin and 3 parts of epoxidized soybean oil, when the temperature reaches 80°C, add 6 parts of antimony trioxide, 10 parts of hydrated zinc borate and 14 parts of activated aluminum hydroxide, when the temperature reaches 90°C, add 15 parts of calcined kaolin 10 parts of heavy calcium carbonate and 25 parts of nano-calcium carbonate, when the temperature reaches 100 ° C, add 0.5 parts of stearic acid and 0.5 parts of butyl stearate, when the temperature reaches 110 ° C, stop high-speed mixing. Unload the material into the low-speed mixer for low-speed mixing and cooling, unload the cooled material into the hopper elevator, add it to the twin-screw extruder for mixing, extrude, granulate and pack.
Embodiment 3
[0026] First put (the following are parts by weight) 100 parts of polyvinyl chloride and 7 parts of stabilizer into a high-speed mixer for high-speed mixing. When the temperature rises to 60 ° C, add 45 parts of plasticizer UN488, 10 parts of long-chain chlorine Chemical paraffin and 5 parts of epoxidized soybean oil, when the temperature reaches 80°C, add 4 parts of antimony trioxide, 6 parts of hydrated zinc borate and 10 parts of activated aluminum hydroxide, when the temperature reaches 90°C, add 20 parts of calcined kaolin 10 parts of heavy calcium carbonate and 20 parts of nano calcium carbonate, when the temperature reaches 100 ° C, add 0.7 parts of stearic acid and 0.7 parts of butyl stearate, when the temperature reaches 110 ° C, stop high-speed mixing. Unload the material into the low-speed mixer for low-speed mixing and cooling, unload the cooled material into the hopper elevator, add it to the twin-screw extruder for mixing, extrude, granulate and pack.
PUM
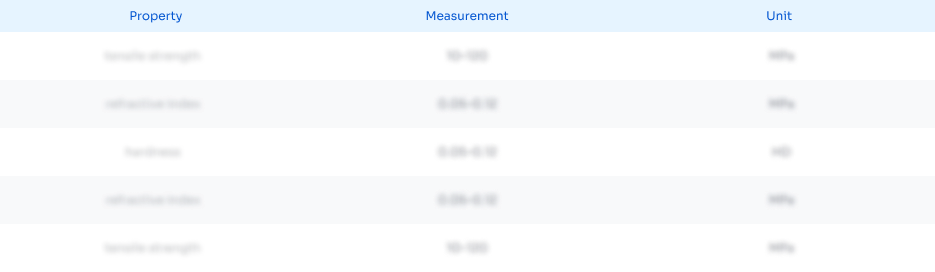
Abstract
Description
Claims
Application Information

- R&D
- Intellectual Property
- Life Sciences
- Materials
- Tech Scout
- Unparalleled Data Quality
- Higher Quality Content
- 60% Fewer Hallucinations
Browse by: Latest US Patents, China's latest patents, Technical Efficacy Thesaurus, Application Domain, Technology Topic, Popular Technical Reports.
© 2025 PatSnap. All rights reserved.Legal|Privacy policy|Modern Slavery Act Transparency Statement|Sitemap|About US| Contact US: help@patsnap.com