Temperature control method for molding equipment used in glass substrate production
A temperature control method and production process technology, which are applied in glass forming, glass forming, glass manufacturing equipment, etc., can solve the problems of adverse effects of temperature field in forming area, affecting the life of overflow device, and rising temperature of the upper part of overflow device.
- Summary
- Abstract
- Description
- Claims
- Application Information
AI Technical Summary
Problems solved by technology
Method used
Image
Examples
Embodiment
[0025] Refer to attached Figure 1-3 , Install a water-cooled coil on the top of the overflow device shell, add temperature sensors and flow sensors at the water inlet and outlet of the water-cooled coil, and adjust in time according to the temperature at the top of the overflow device to ensure the up and down of the overflow device The internal temperature difference is within the acceptable range. At the same time, it is also ensured that the temperature at the top of the overflow device is higher than that at the bottom, and that the overflow device is in a qualified temperature field, ensuring that the forming temperature field of the molten glass is high at the top and low at the bottom, while maintaining a reasonable temperature gradient.
PUM
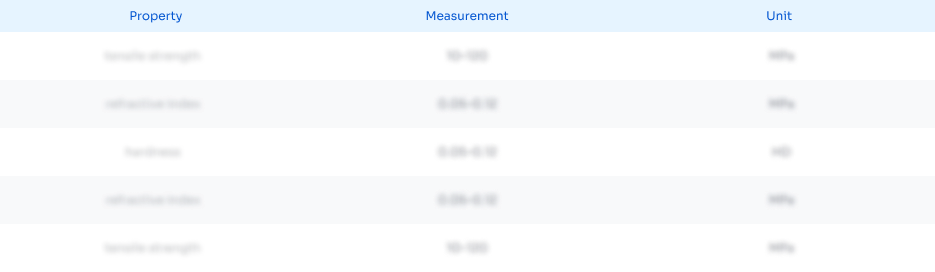
Abstract
Description
Claims
Application Information

- R&D
- Intellectual Property
- Life Sciences
- Materials
- Tech Scout
- Unparalleled Data Quality
- Higher Quality Content
- 60% Fewer Hallucinations
Browse by: Latest US Patents, China's latest patents, Technical Efficacy Thesaurus, Application Domain, Technology Topic, Popular Technical Reports.
© 2025 PatSnap. All rights reserved.Legal|Privacy policy|Modern Slavery Act Transparency Statement|Sitemap|About US| Contact US: help@patsnap.com